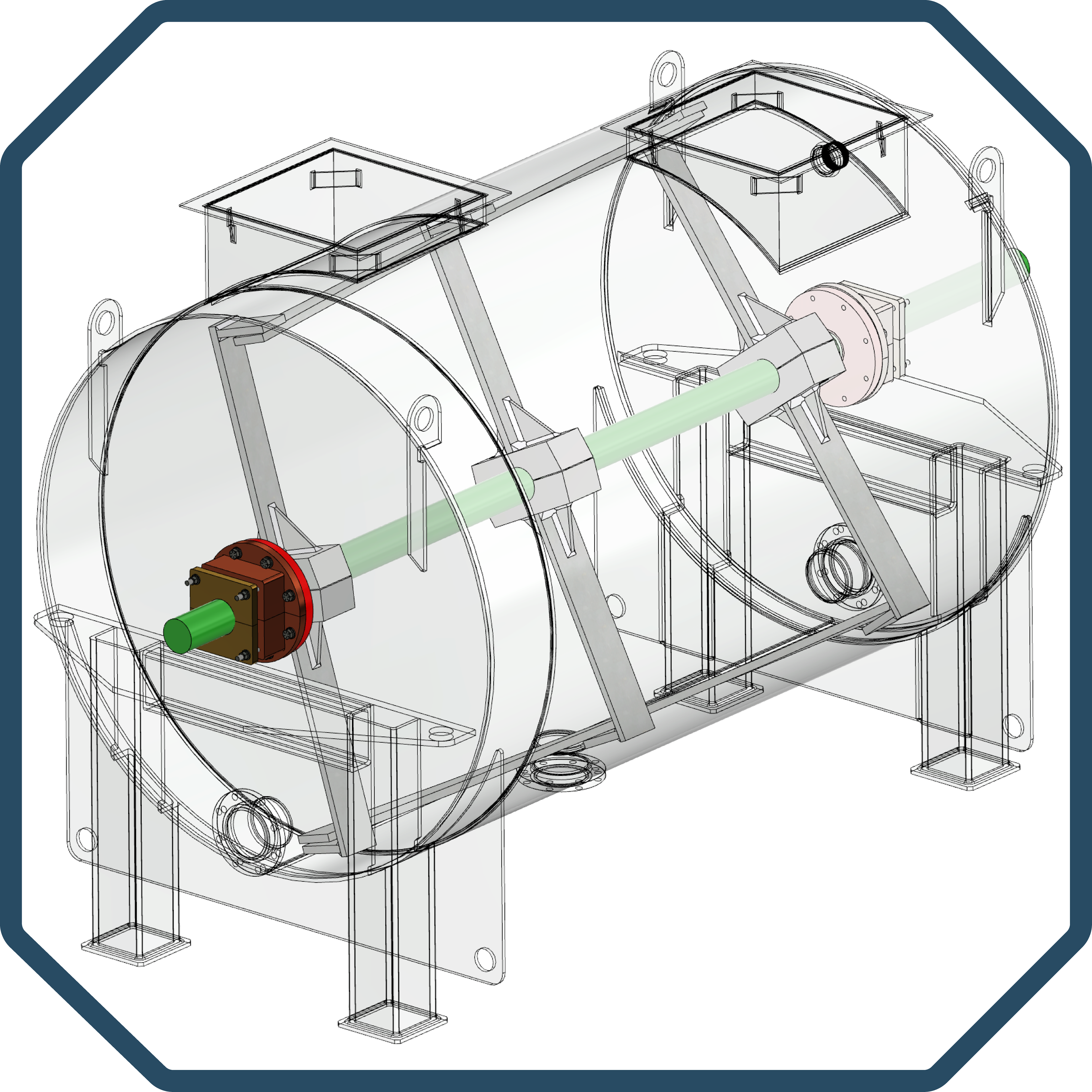
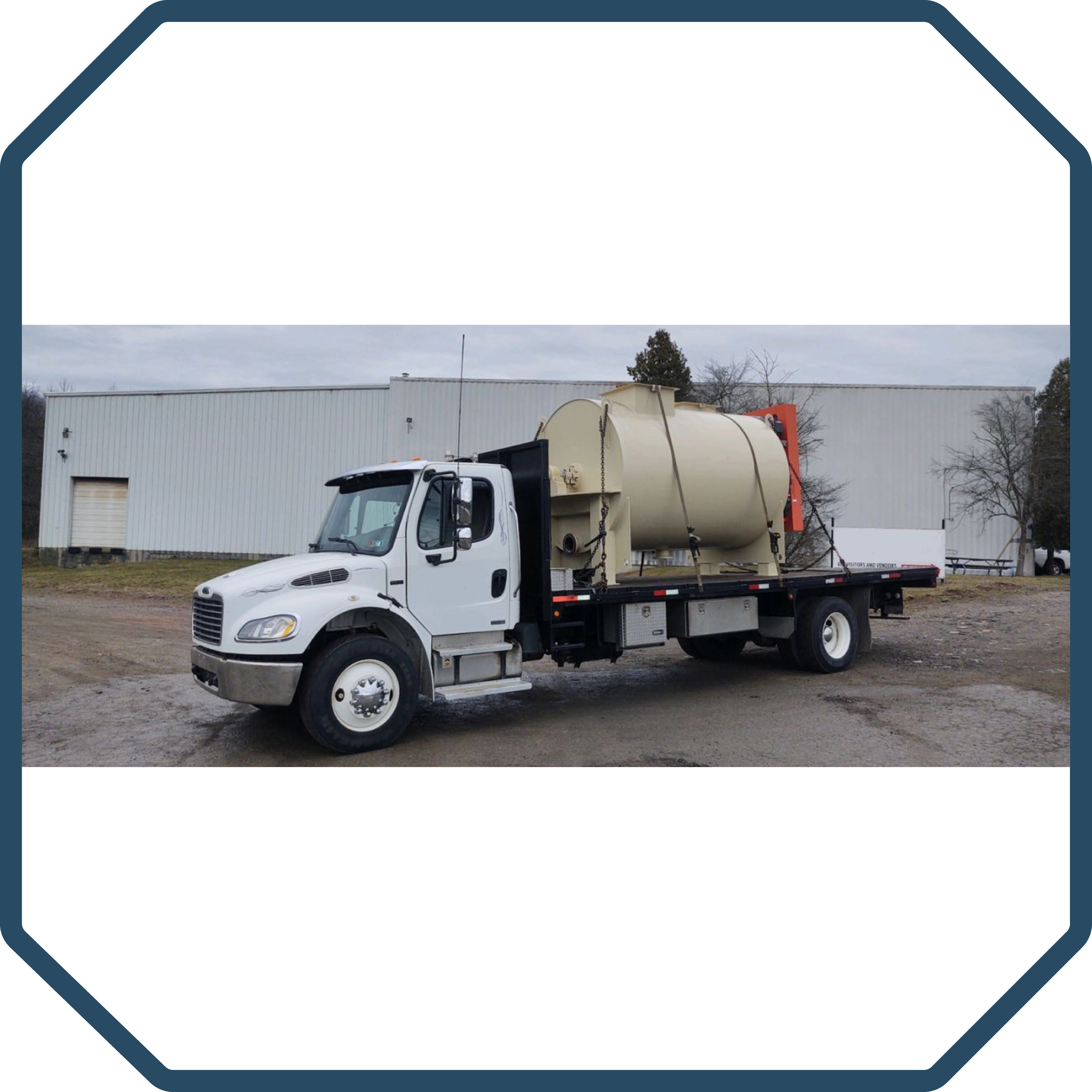
ABOUT THE CLIENT
Rolling, Tank, and Fabrication, Inc. offers roll and press brake forming, custom fabrications, steel sales and pick-up / delivery services.
INTRODUCTION
This project was brought to Bedrock as an existing solution that needed updated and refined. A local steel fabricator teamed up with a wholesale chocolate manufacturer who wished to expand their facility’s process throughput while simultaneously resolving manufacturing personnel pain points. This job was perfectly suited to Bedrock’s design process and methodology.
The scope of the project required a complete set of mixing tank top-level assembly, weldment, detail, and modification drawings.
The original design documents were unavailable and extensive reverse engineering was performed to develop an updated design for a fully-functioning machine.
The project was further complicated by the need to interface with existing commercial off-the-shelf parts.
Bedrock Design and Craft, LLC traveled to provide the client with additional support through multiple site visits. Time was invested to speak with fabrication personnel to learn about the unique aspects of the supply, rolling, and welding processes required to bring the tank design from CAD and paper drawings to life.
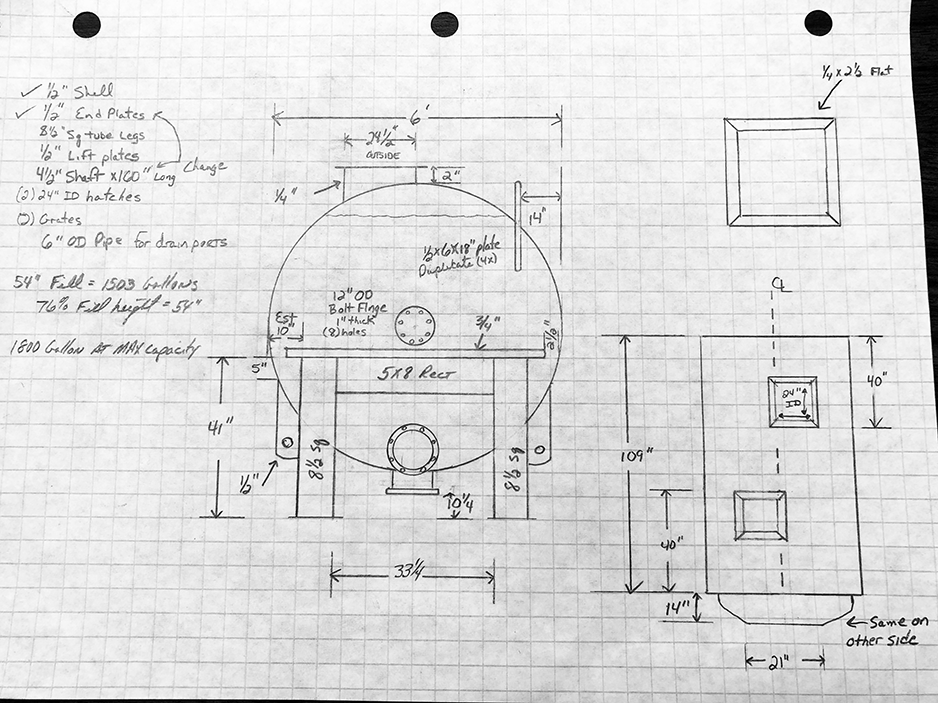
FIELD SURVERY DOCUMENTATION
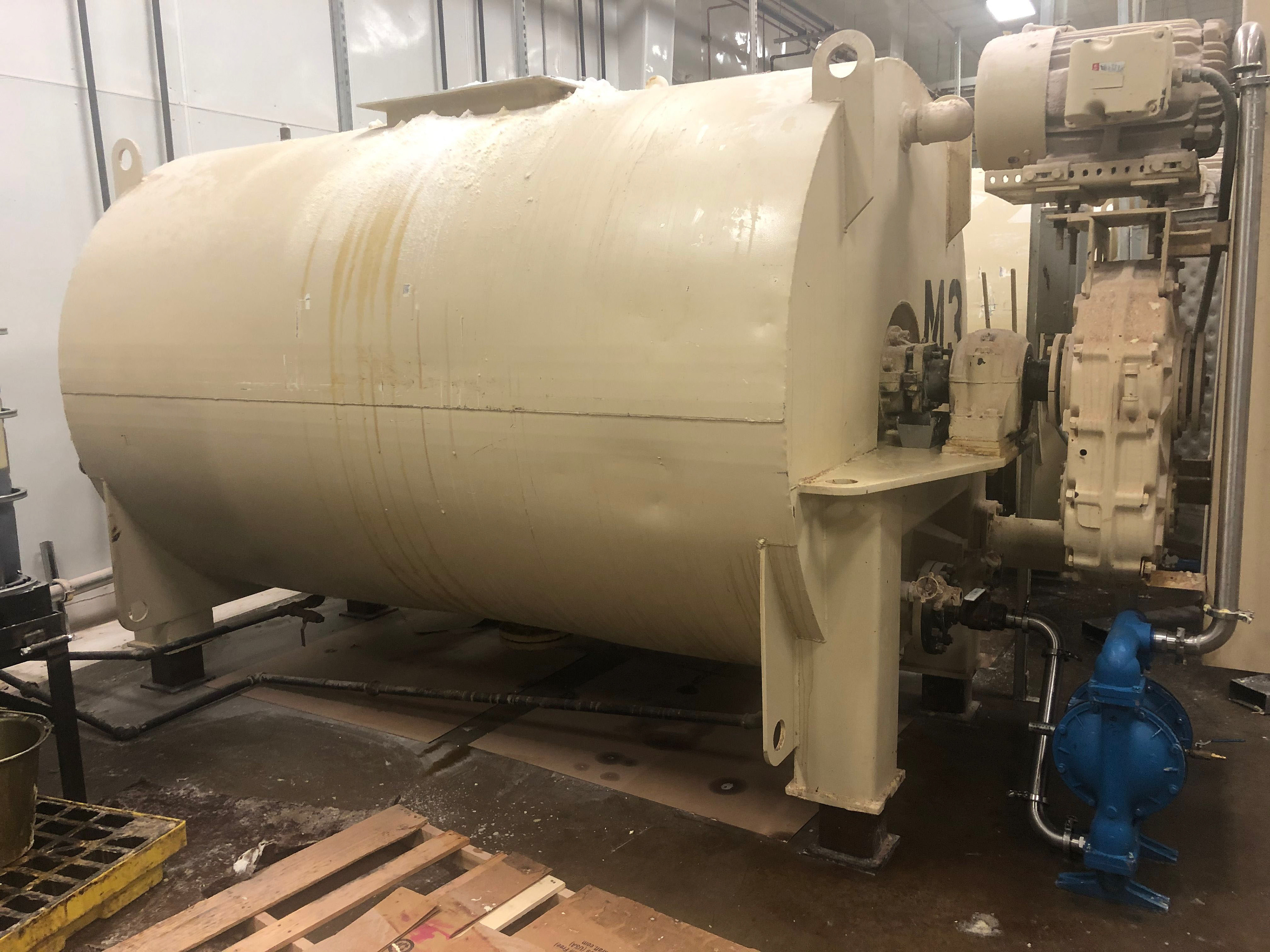
ORIGINAL MIXING TANK DESIGN
DESIGN PROCESS
Using inputs from field surveys, the original tank was measured and photographed extensively to understand the original design intent and updates needed to suit the current factory’s process.
The field survey outputs served as the input to an extensive process of modeling each individual tank part in Autodesk Inventor. Bedrock maintains current licenses specifically to serve clients with this powerful capability.
The tank part models were then joined in an assembly weldment file. This file is programmed with all of the details needed to define each individual weld.
The tank part models were then joined in an assembly weldment file. This file is programmed with all of the details needed to define each individual weld.
The tank weldment model was then brought into a top-level assembly model to show how the commercial-off-the-shelf parts are joined together to form a fully functioning assembly.
The top-level assembly and weldment files were then reviewed with the client to capture comments regarding manufacturing feasibility. From the model files, two dimensional drawings were created for each part, weldment, and assembly and reviewed with the client.
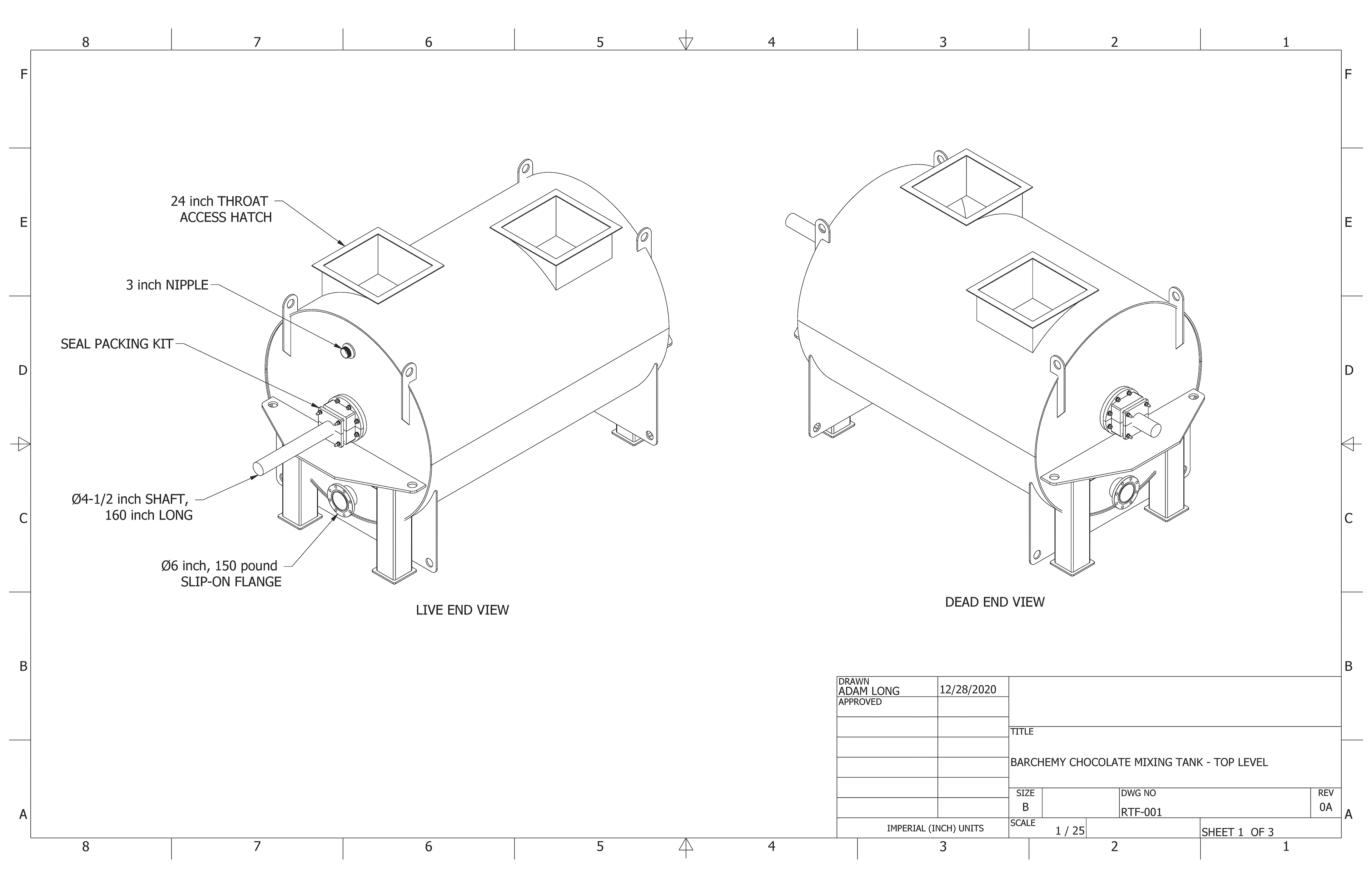
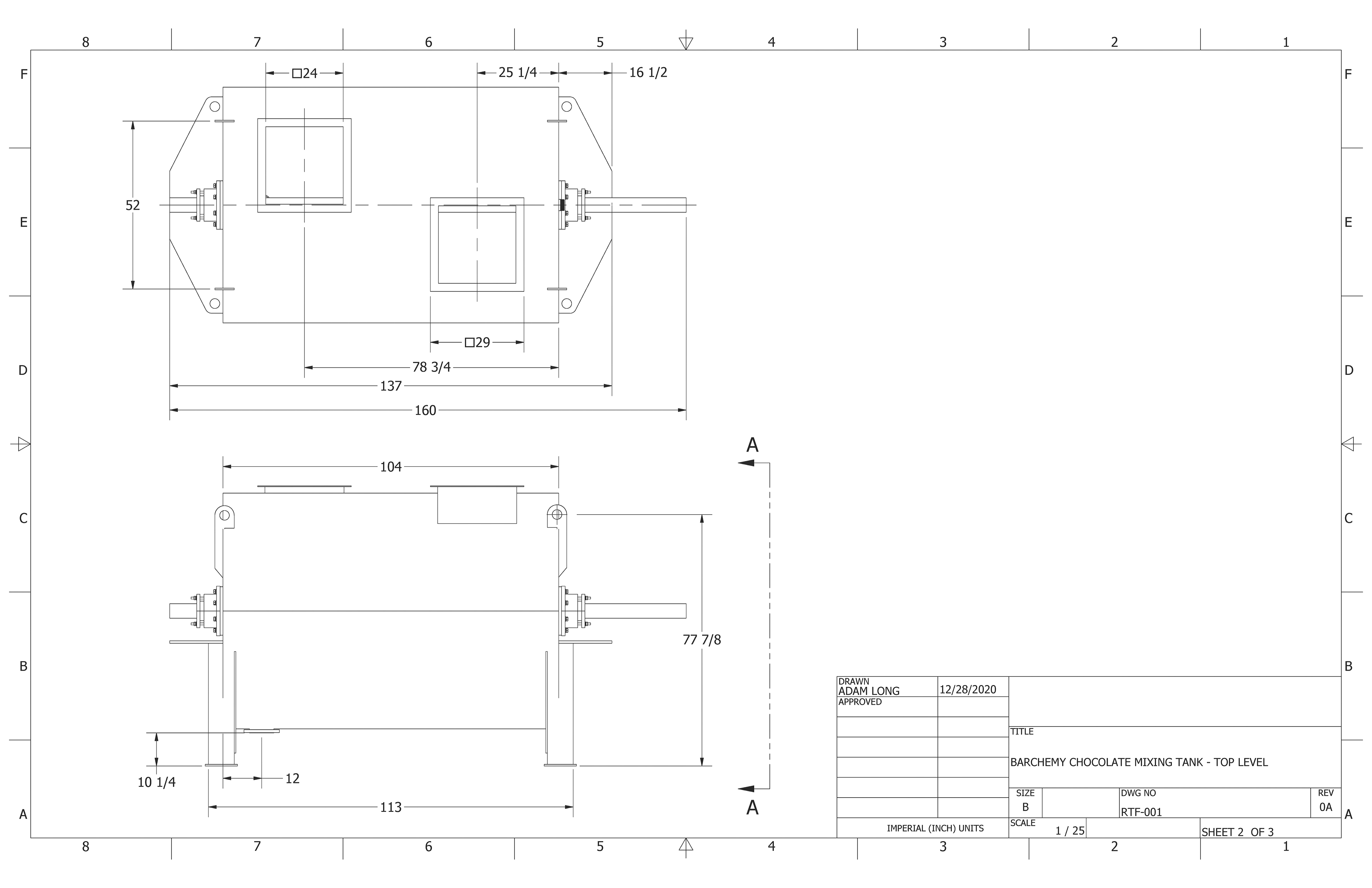
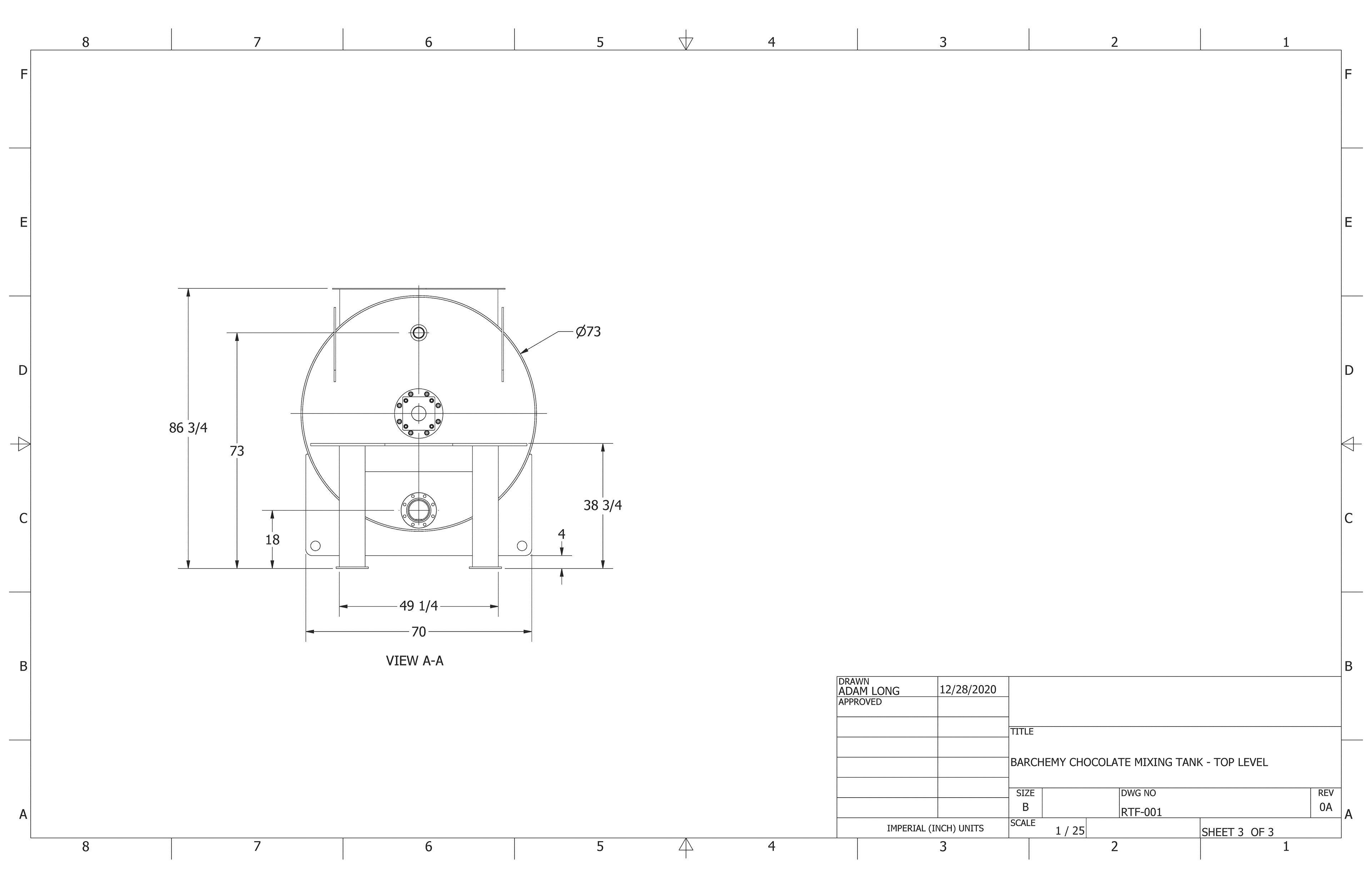
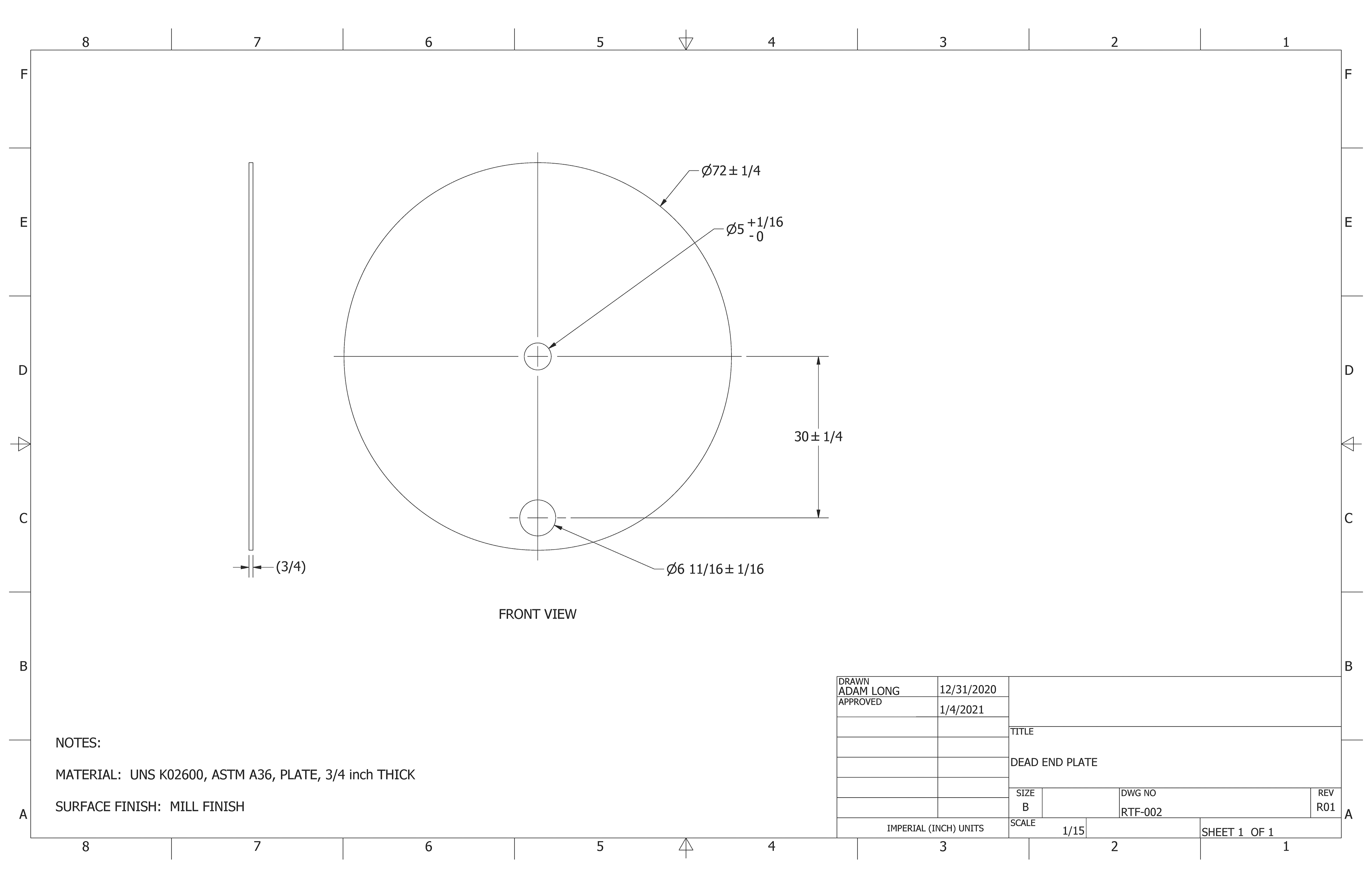
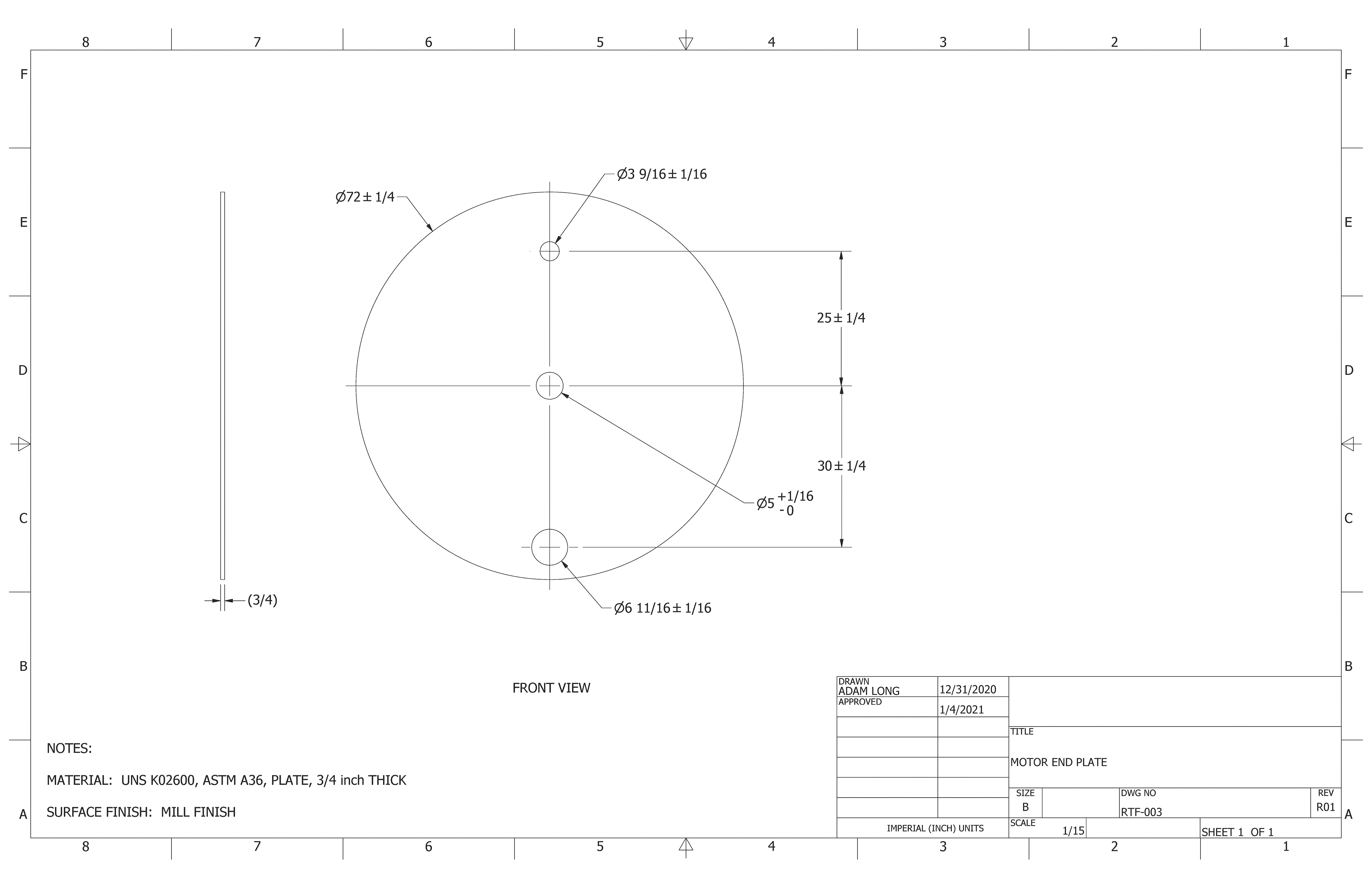
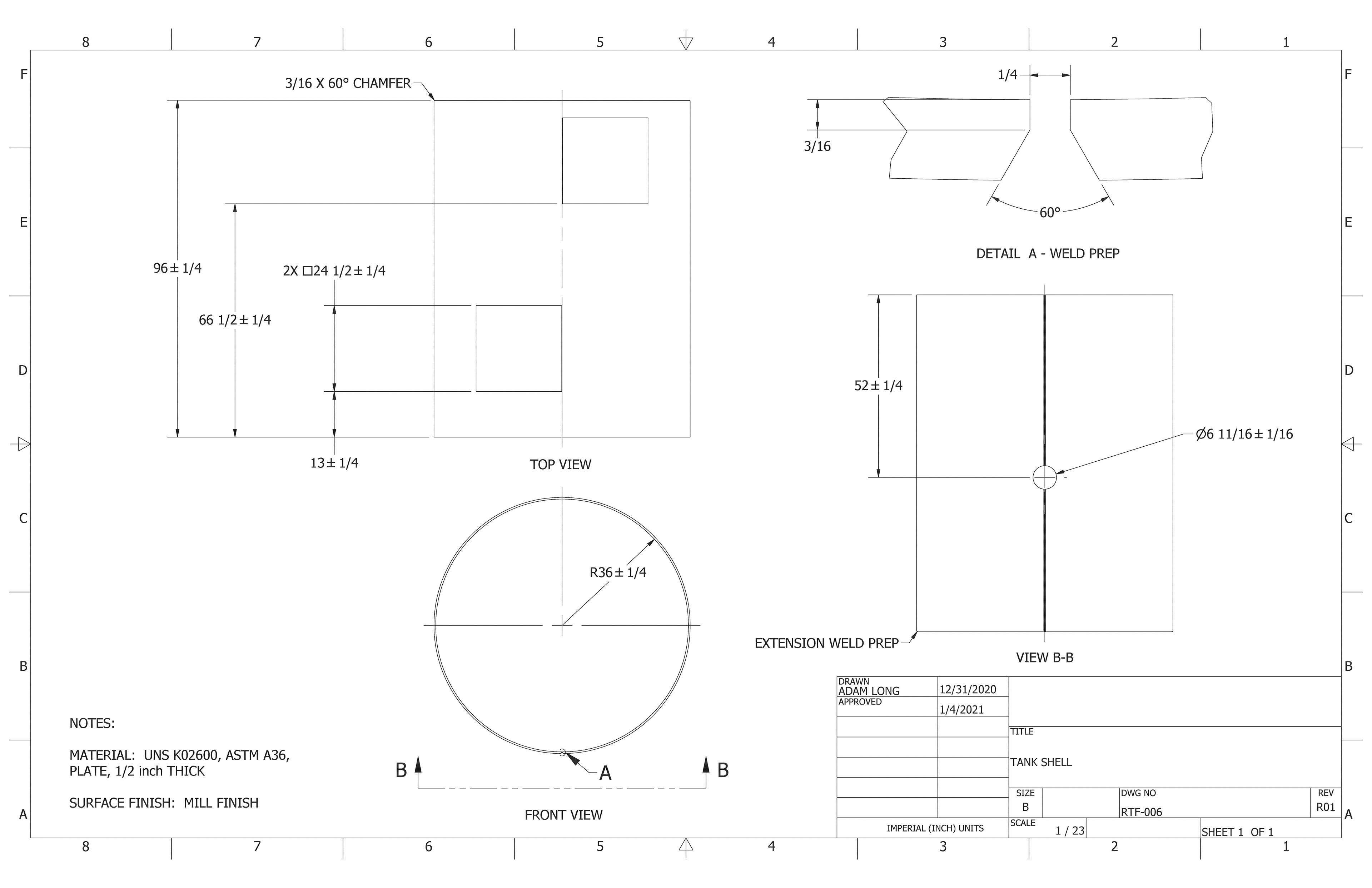
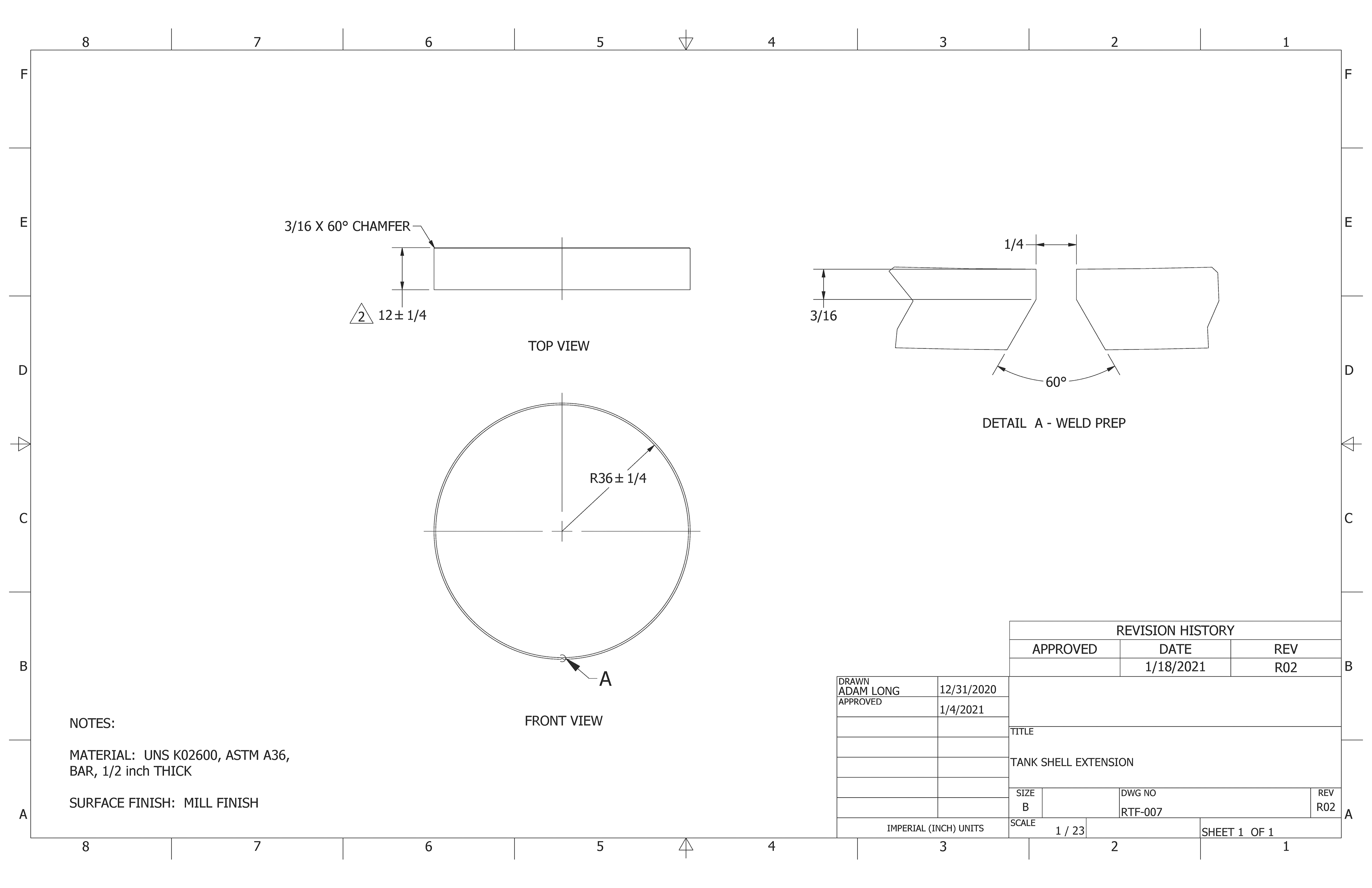
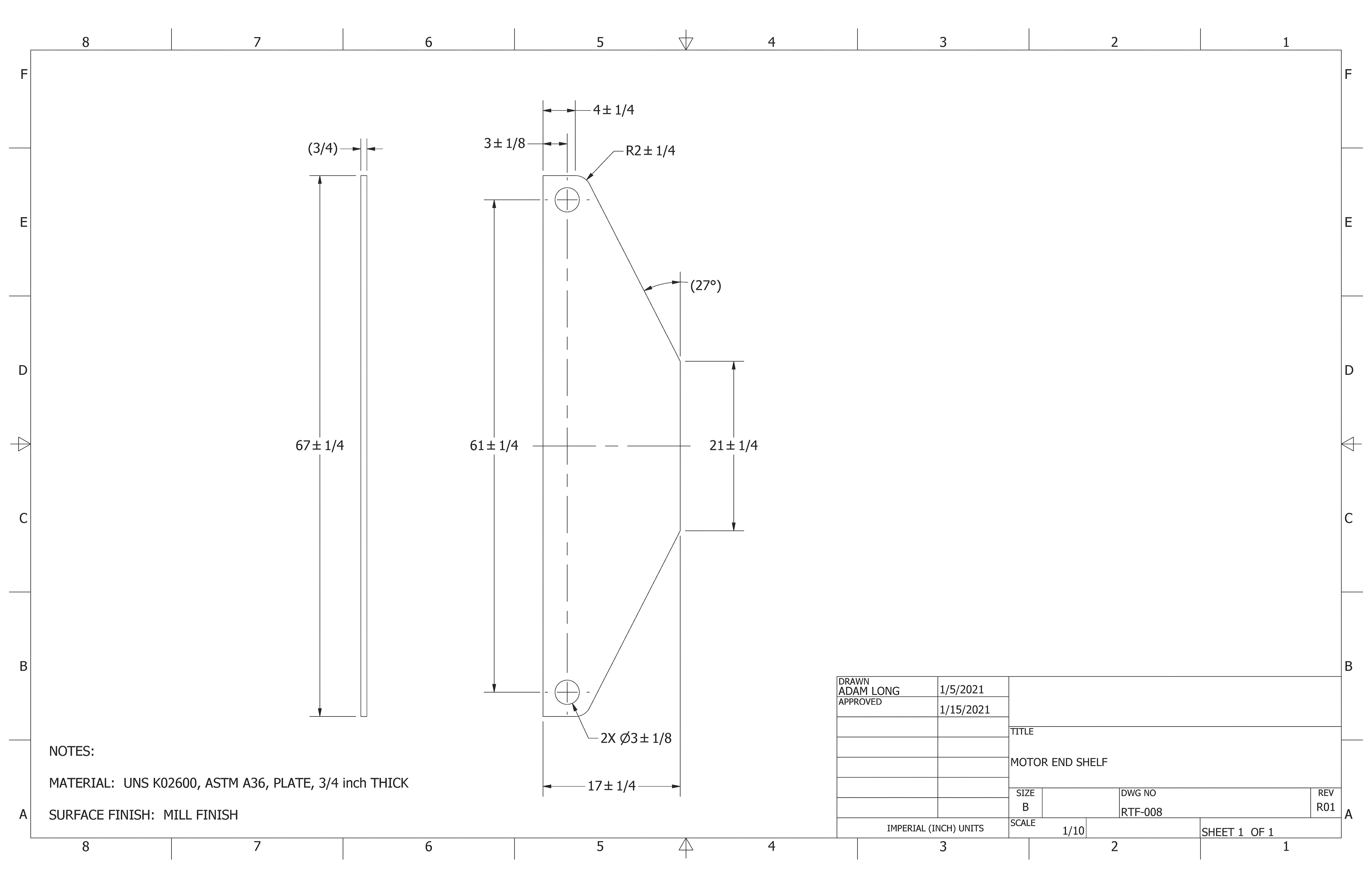
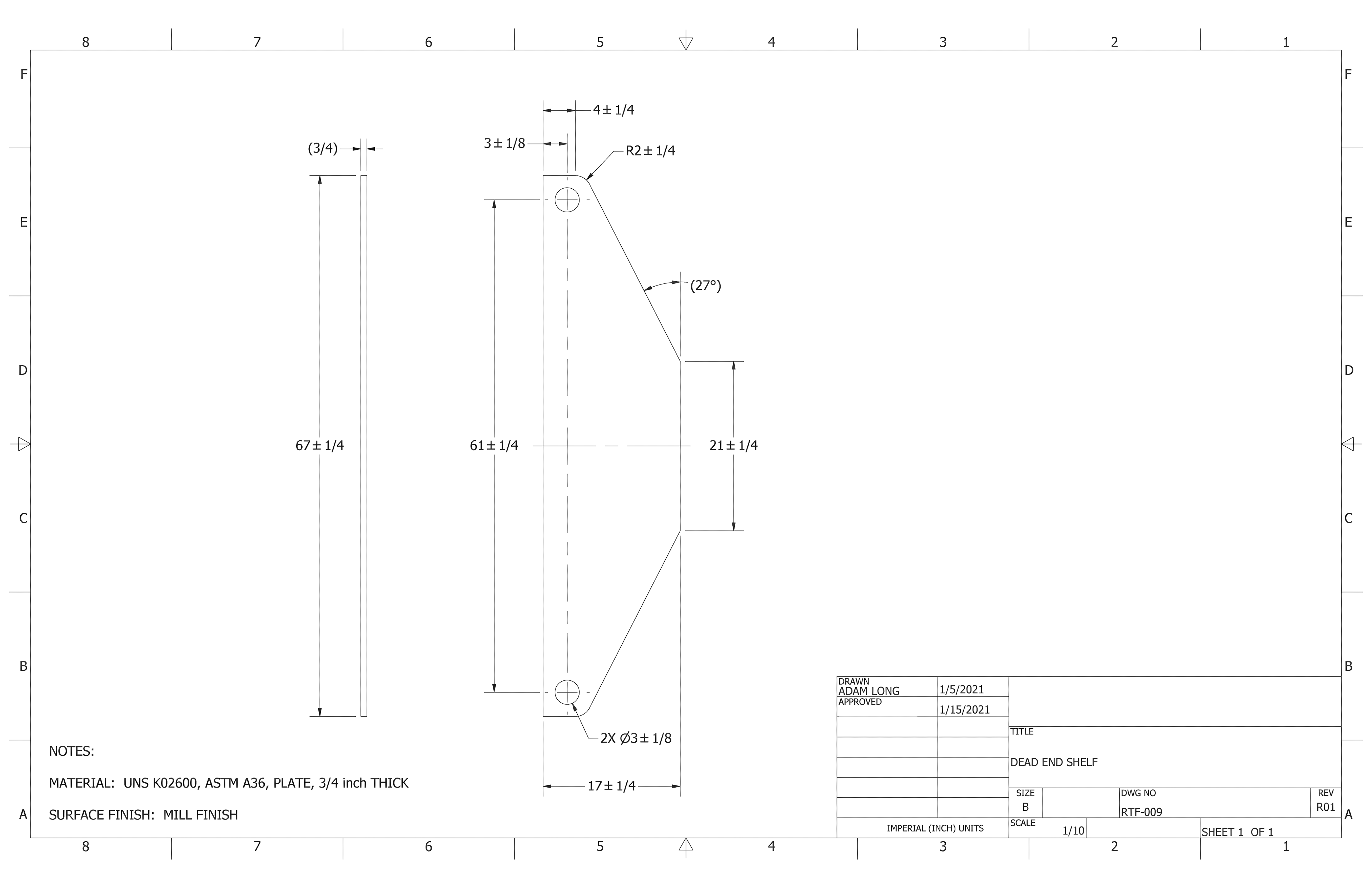
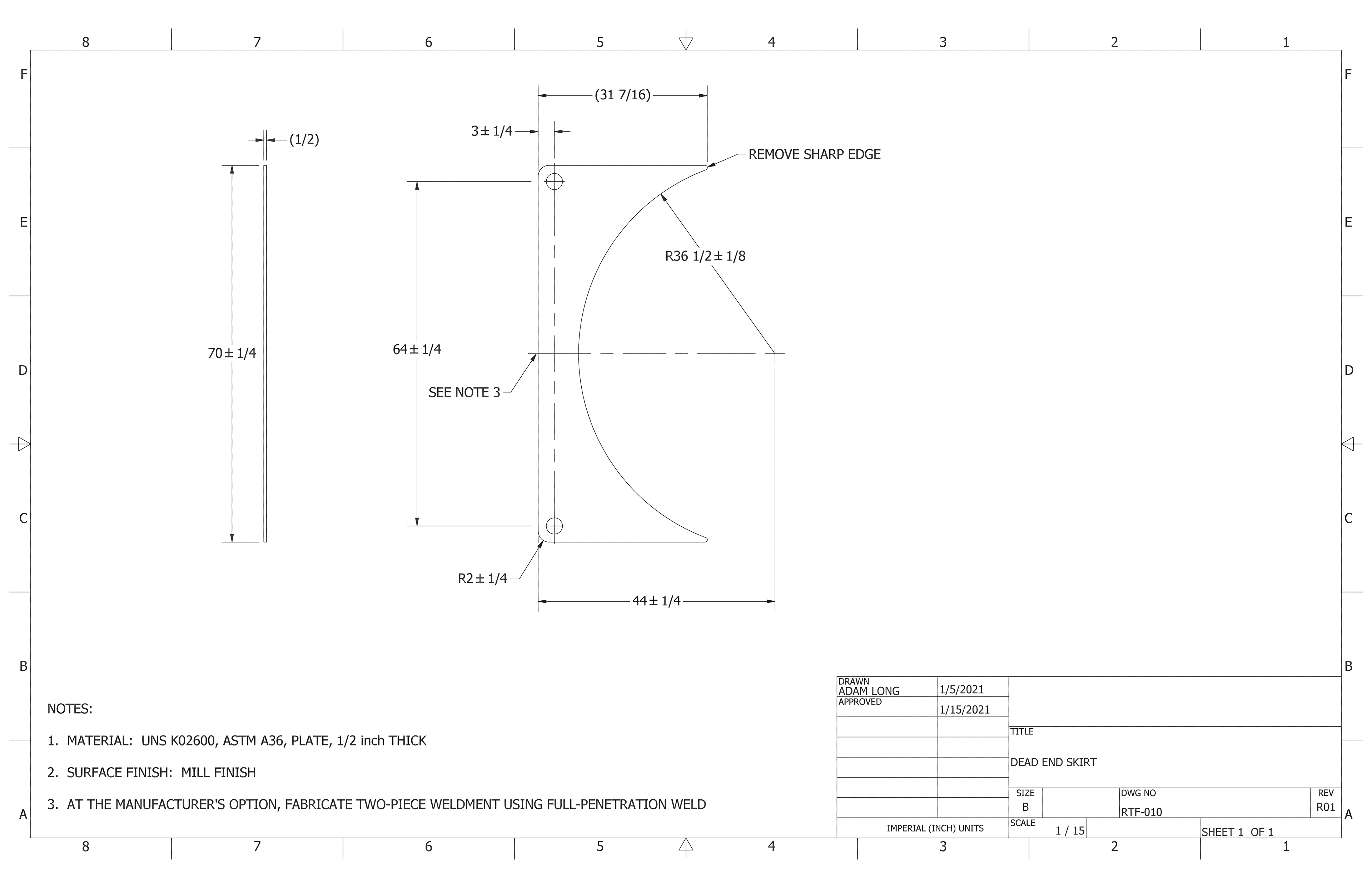
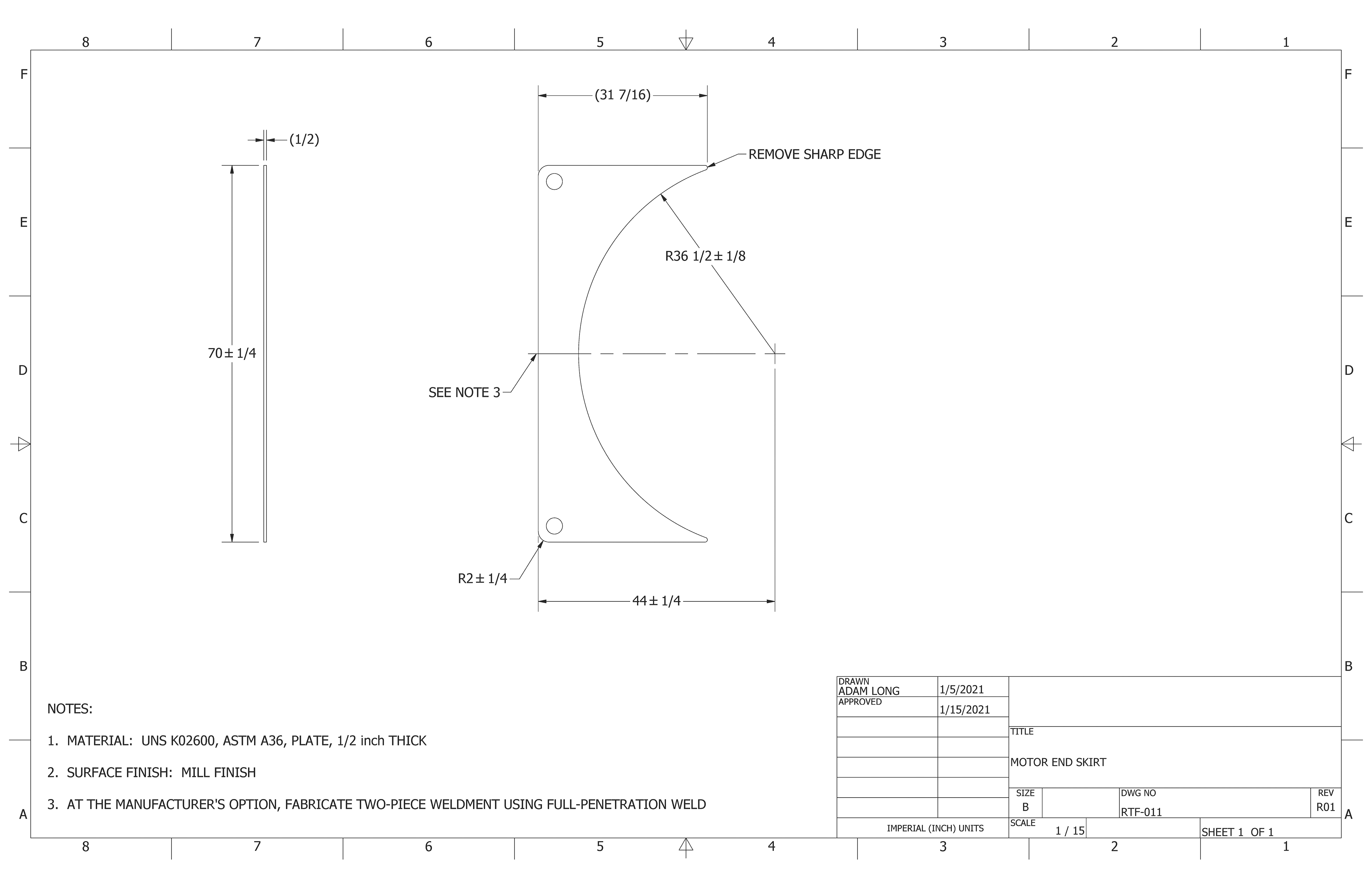
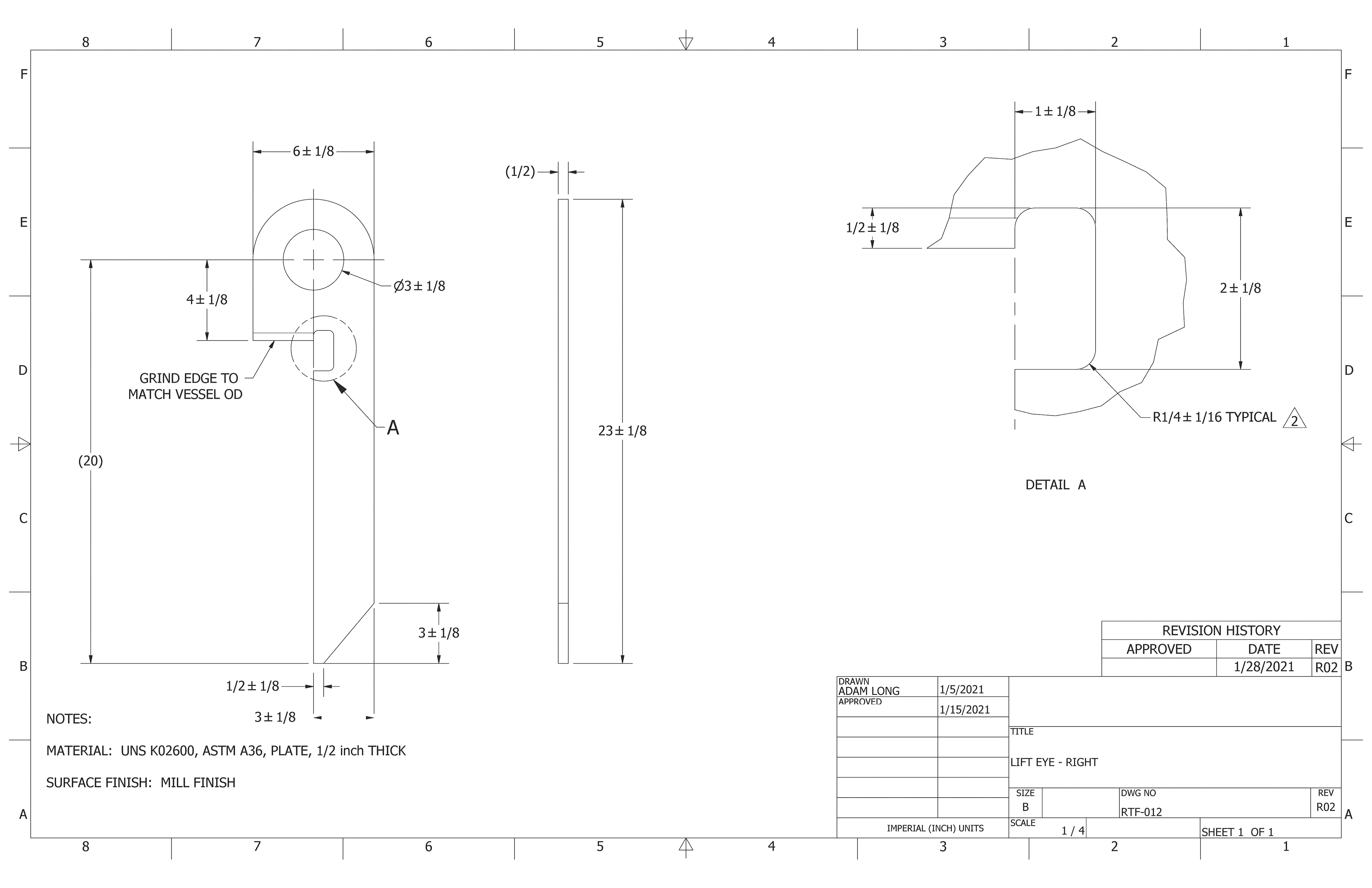
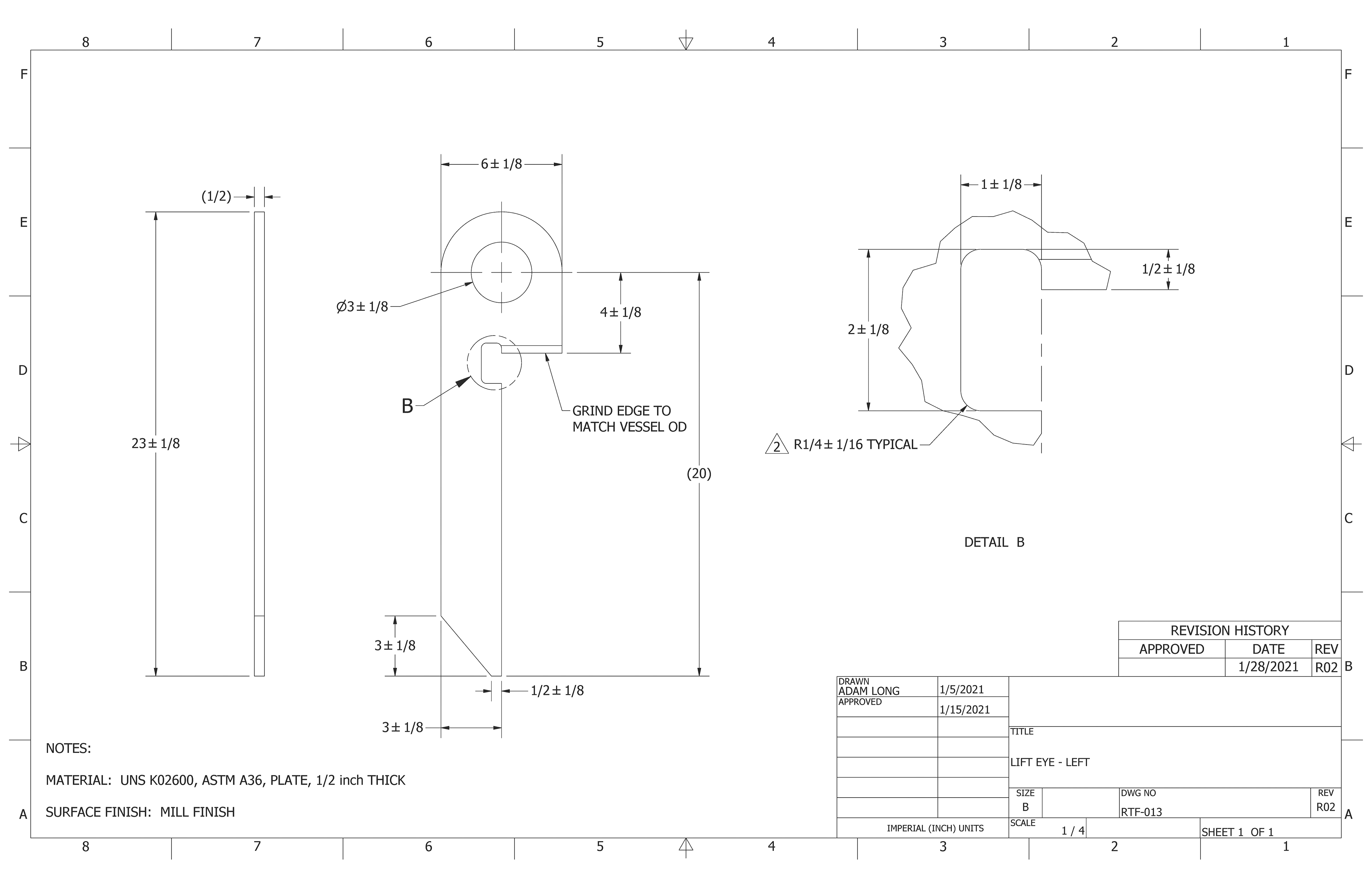
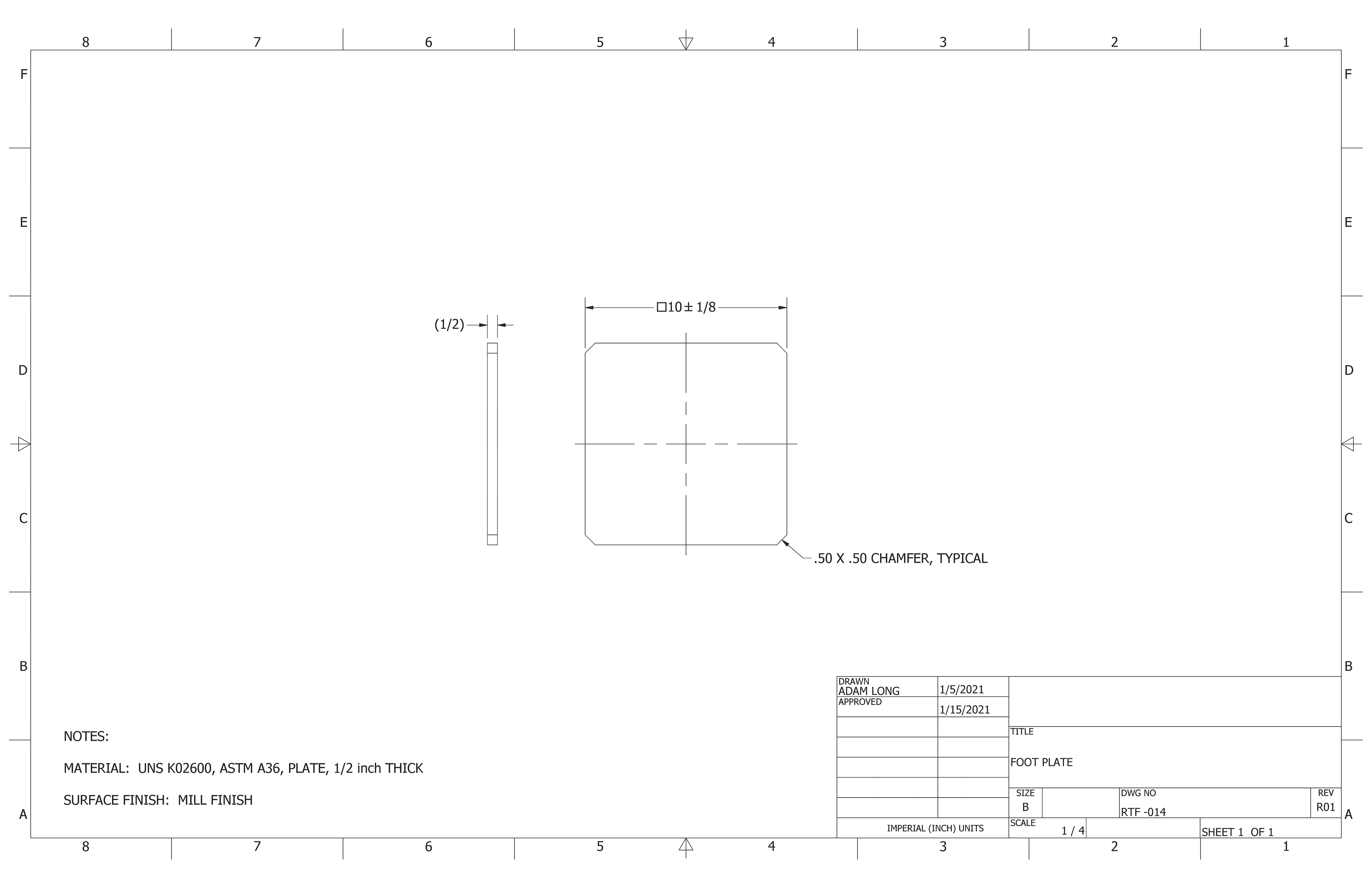
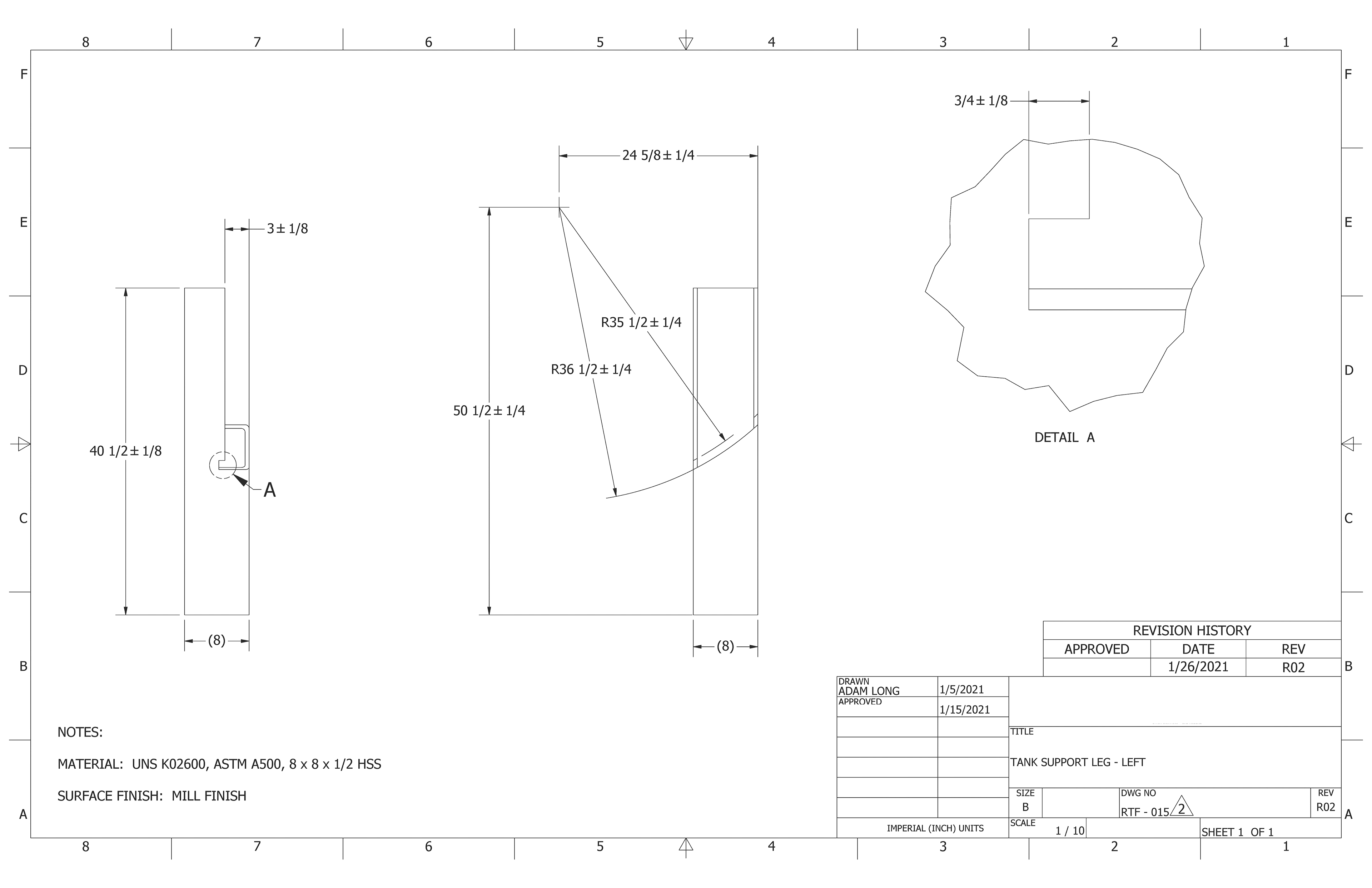
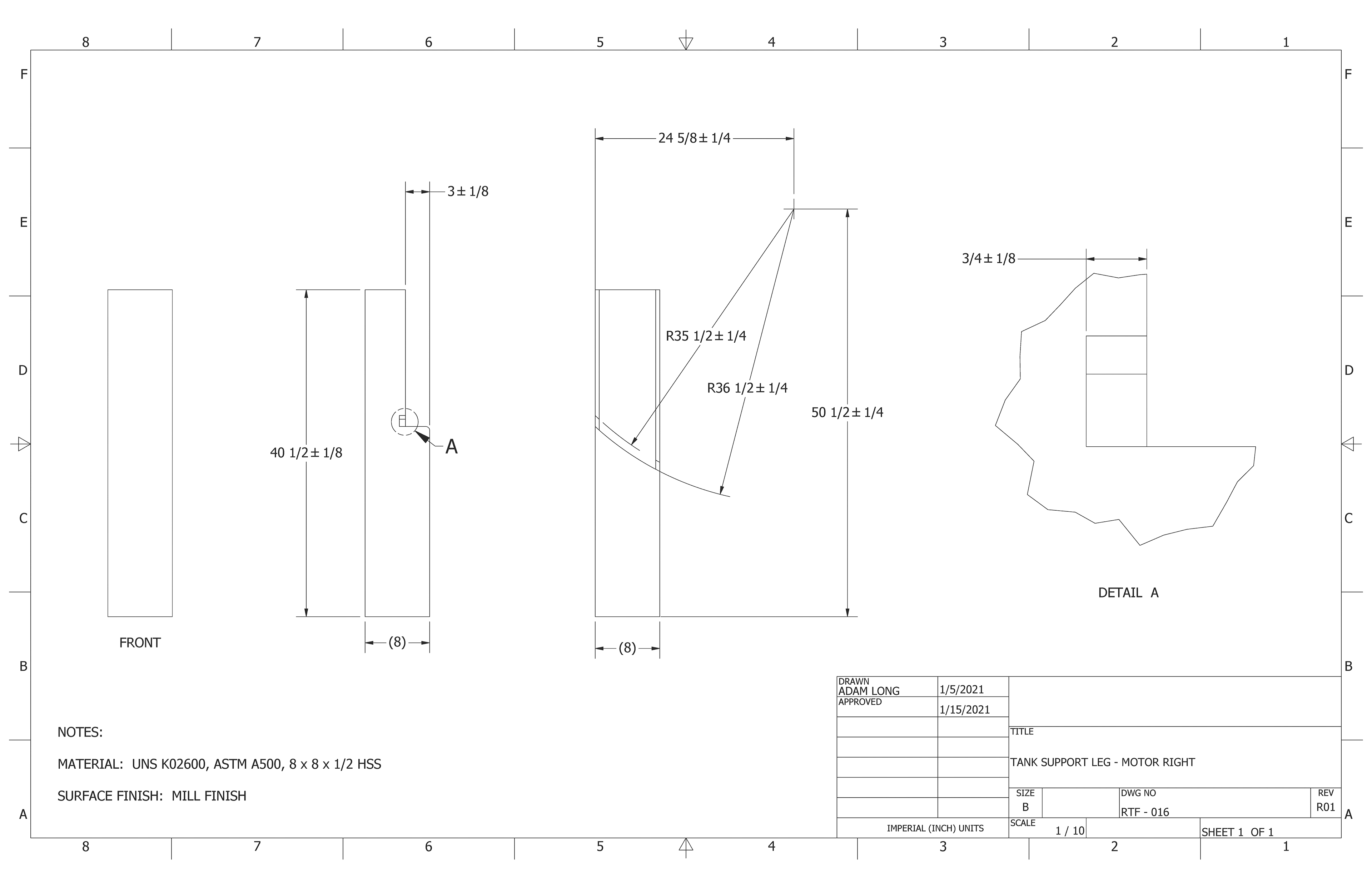
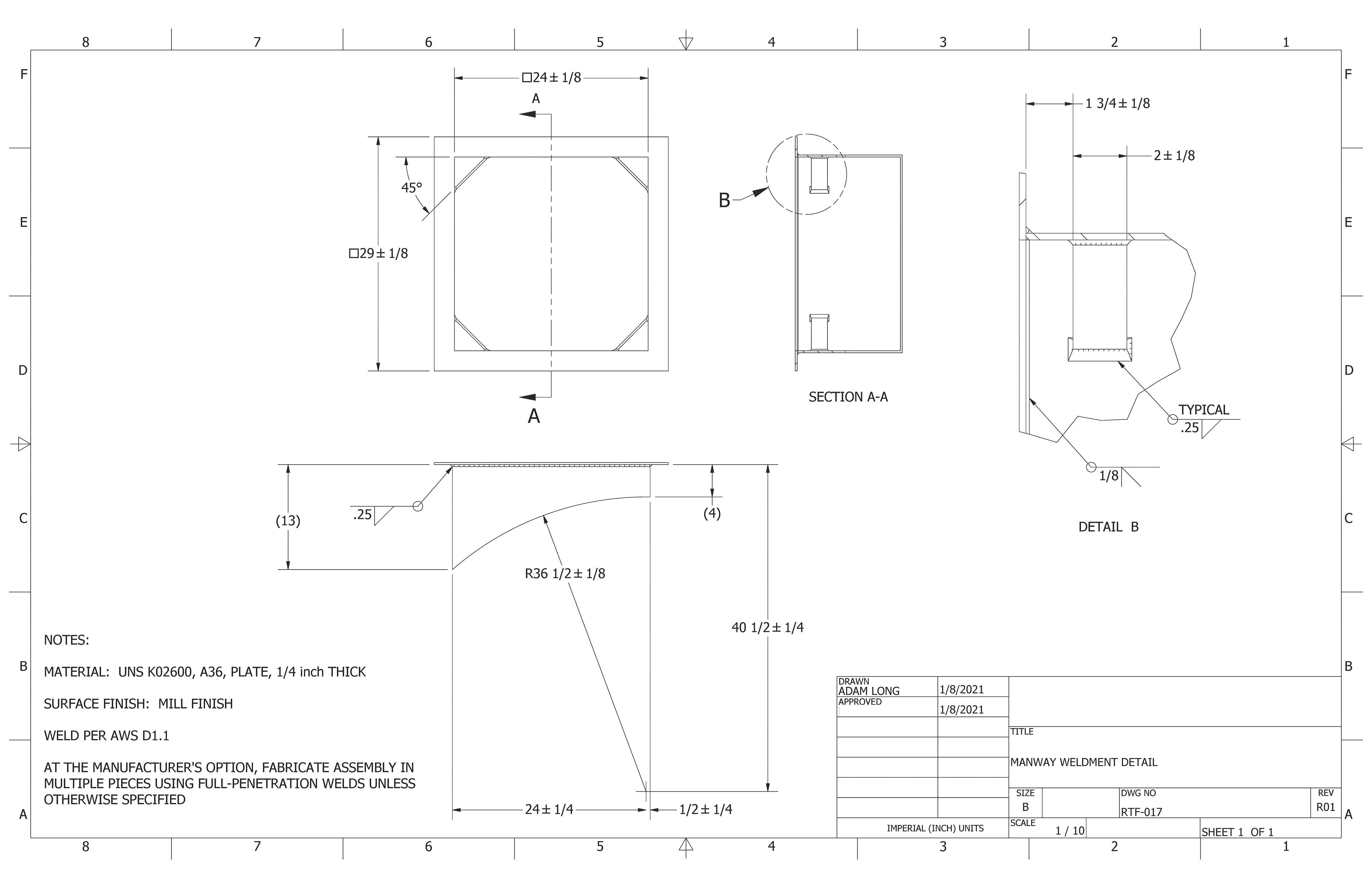
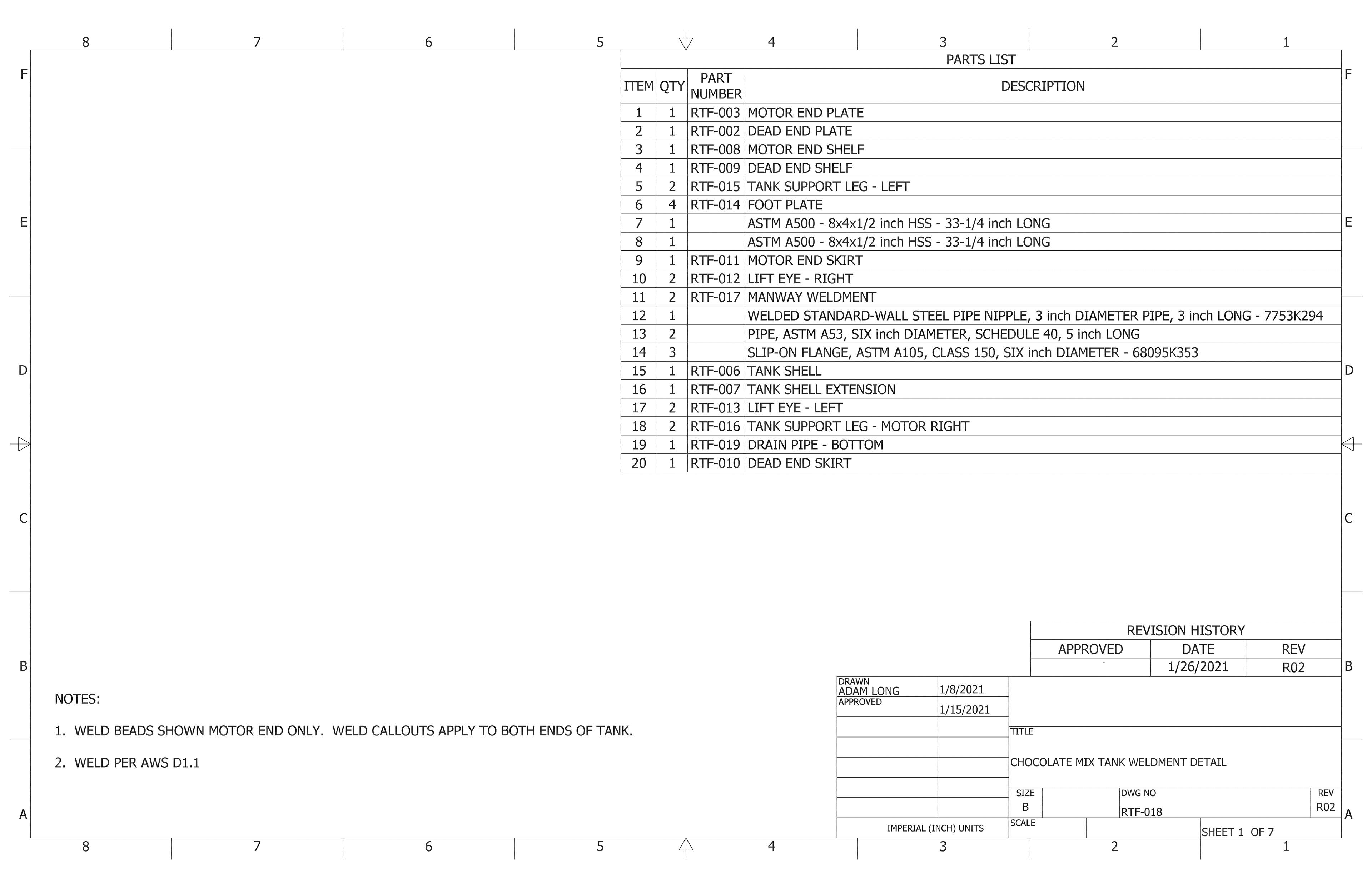
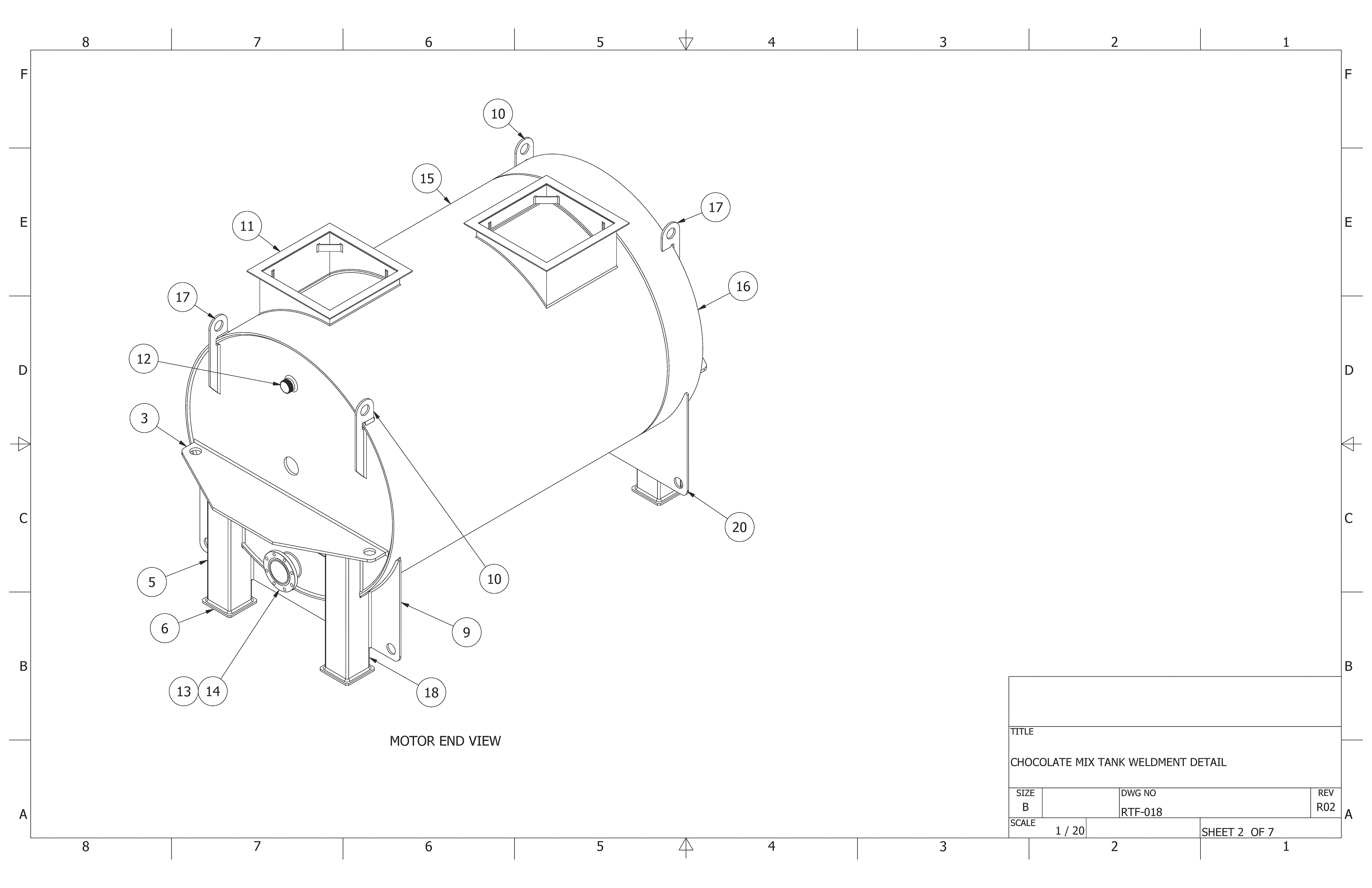
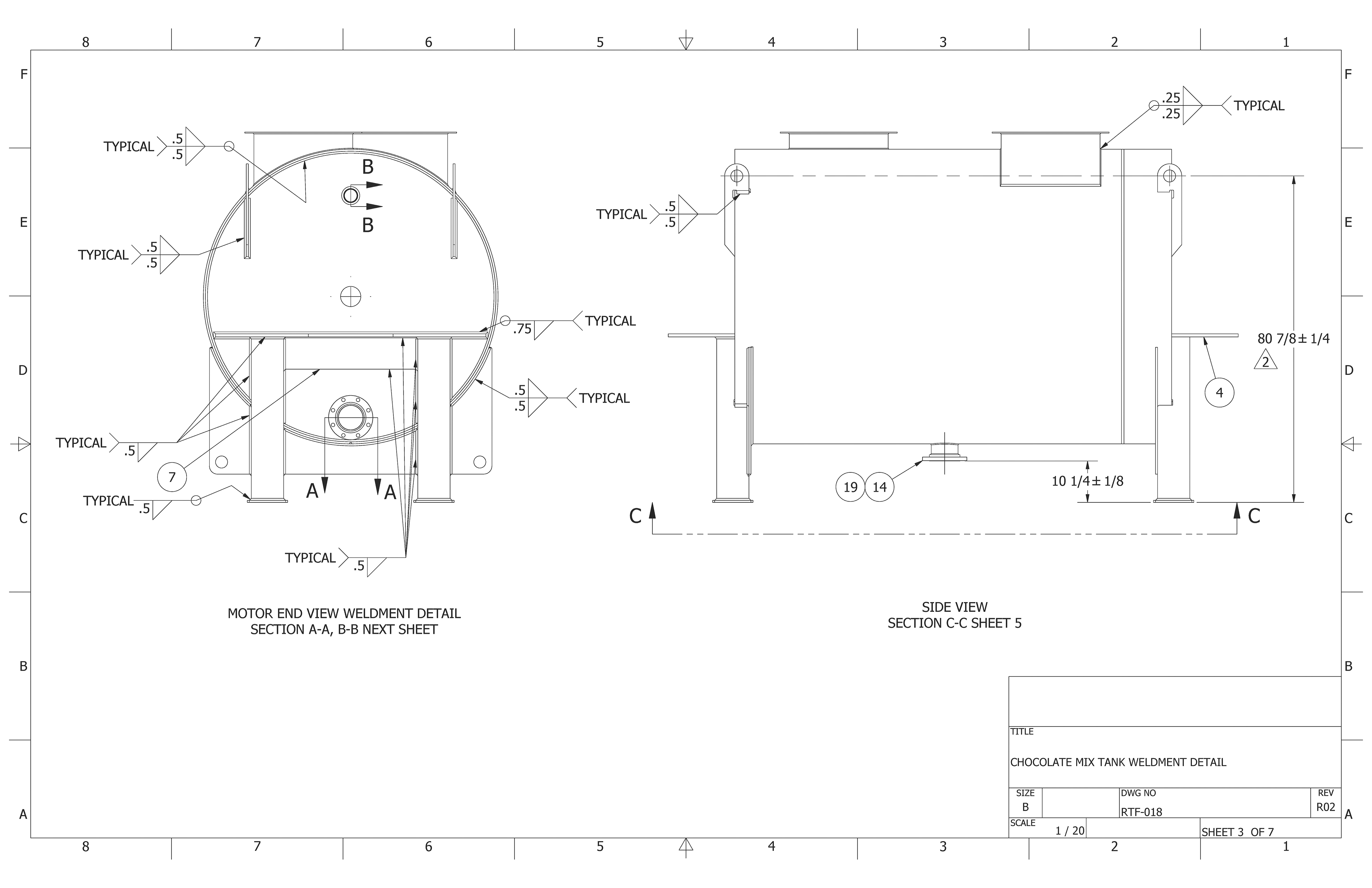
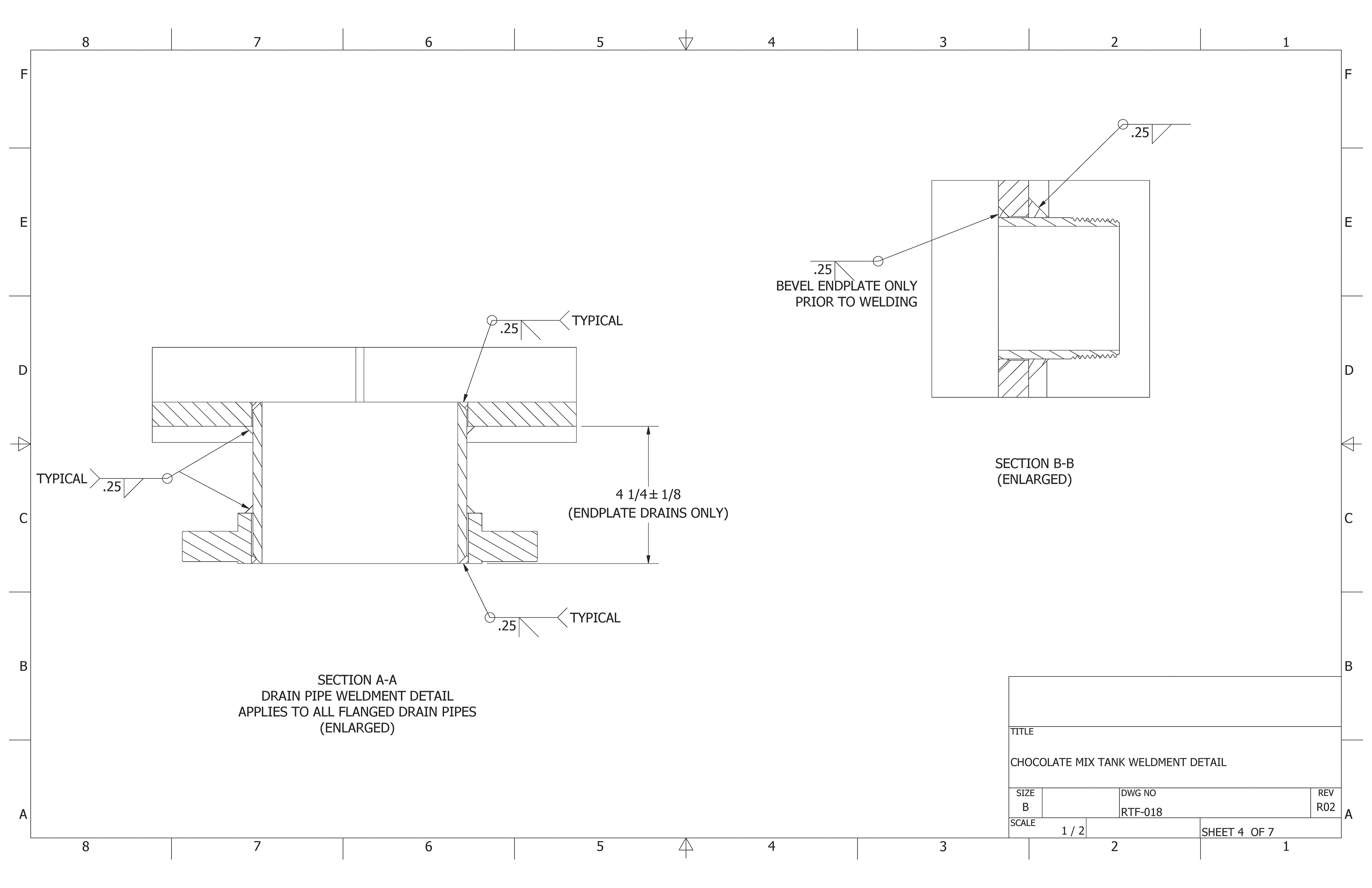
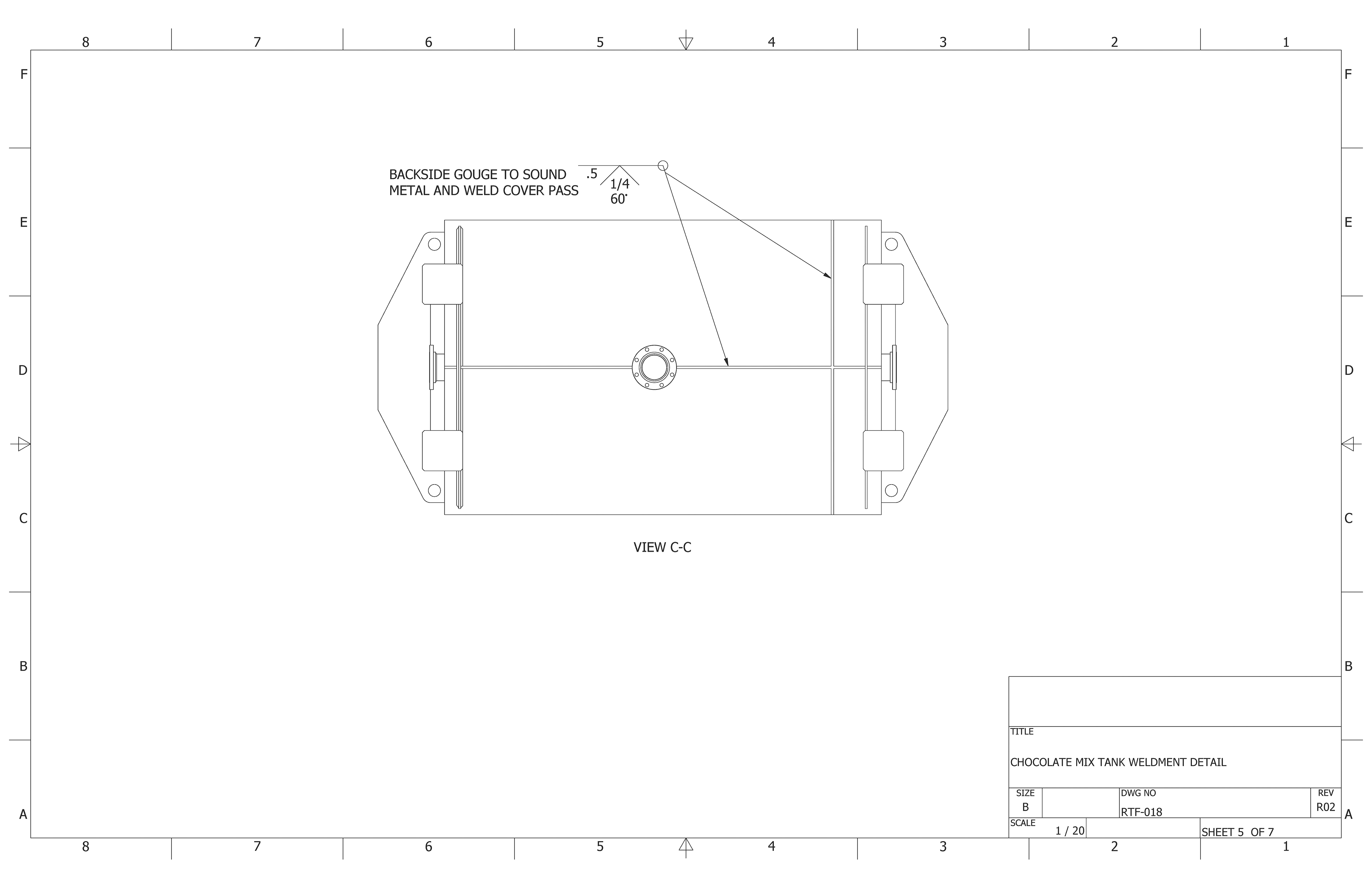
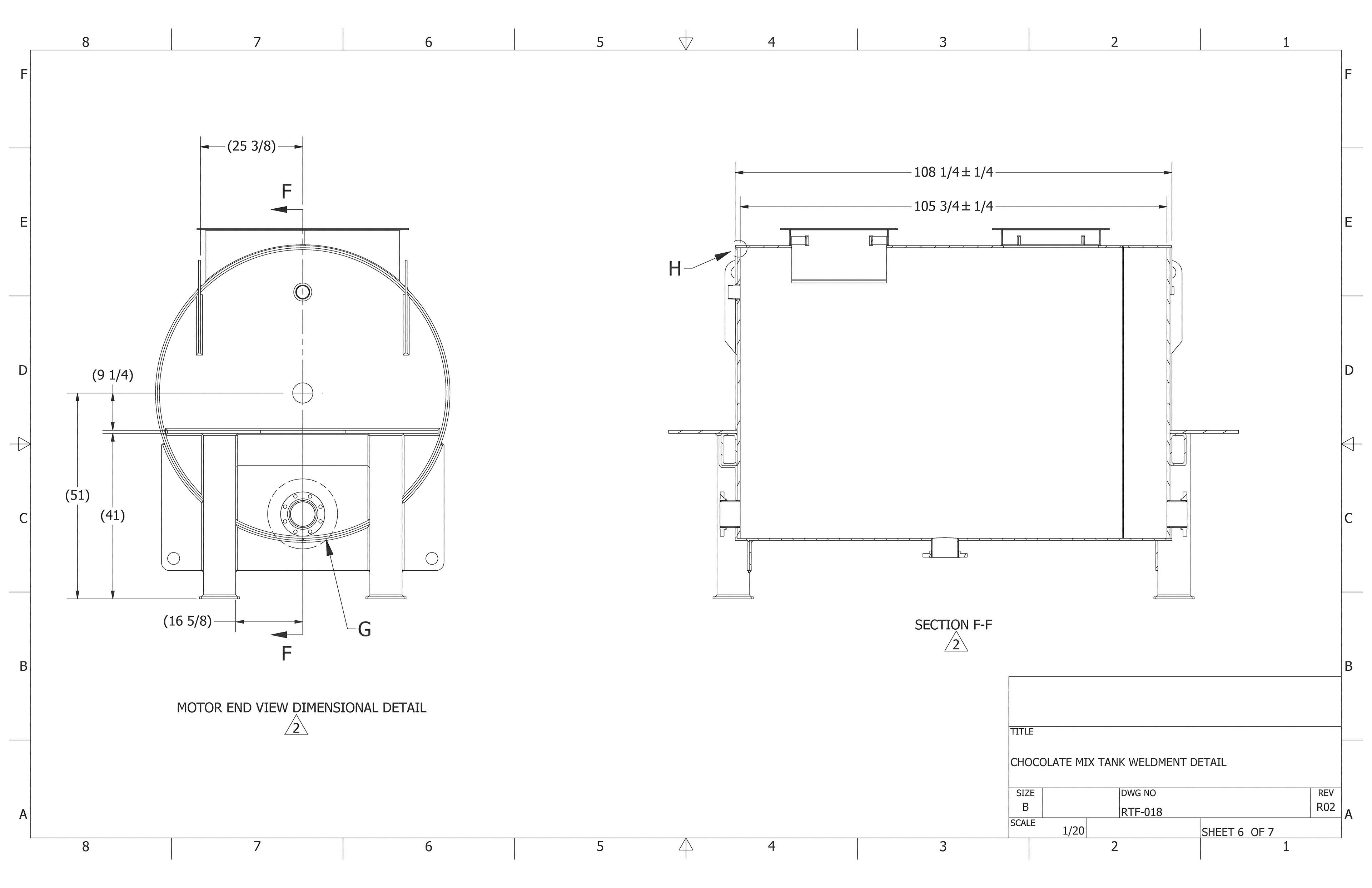
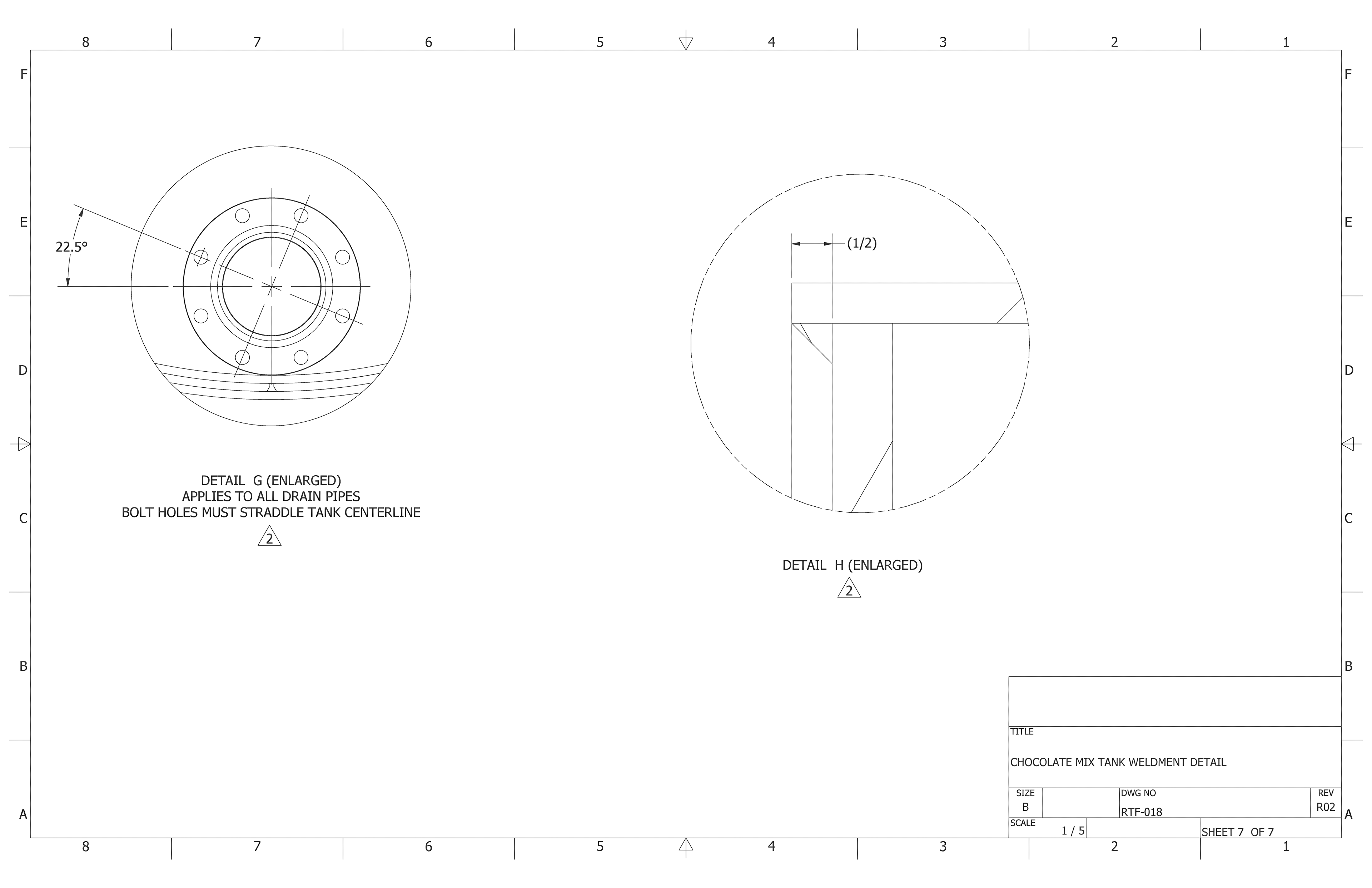
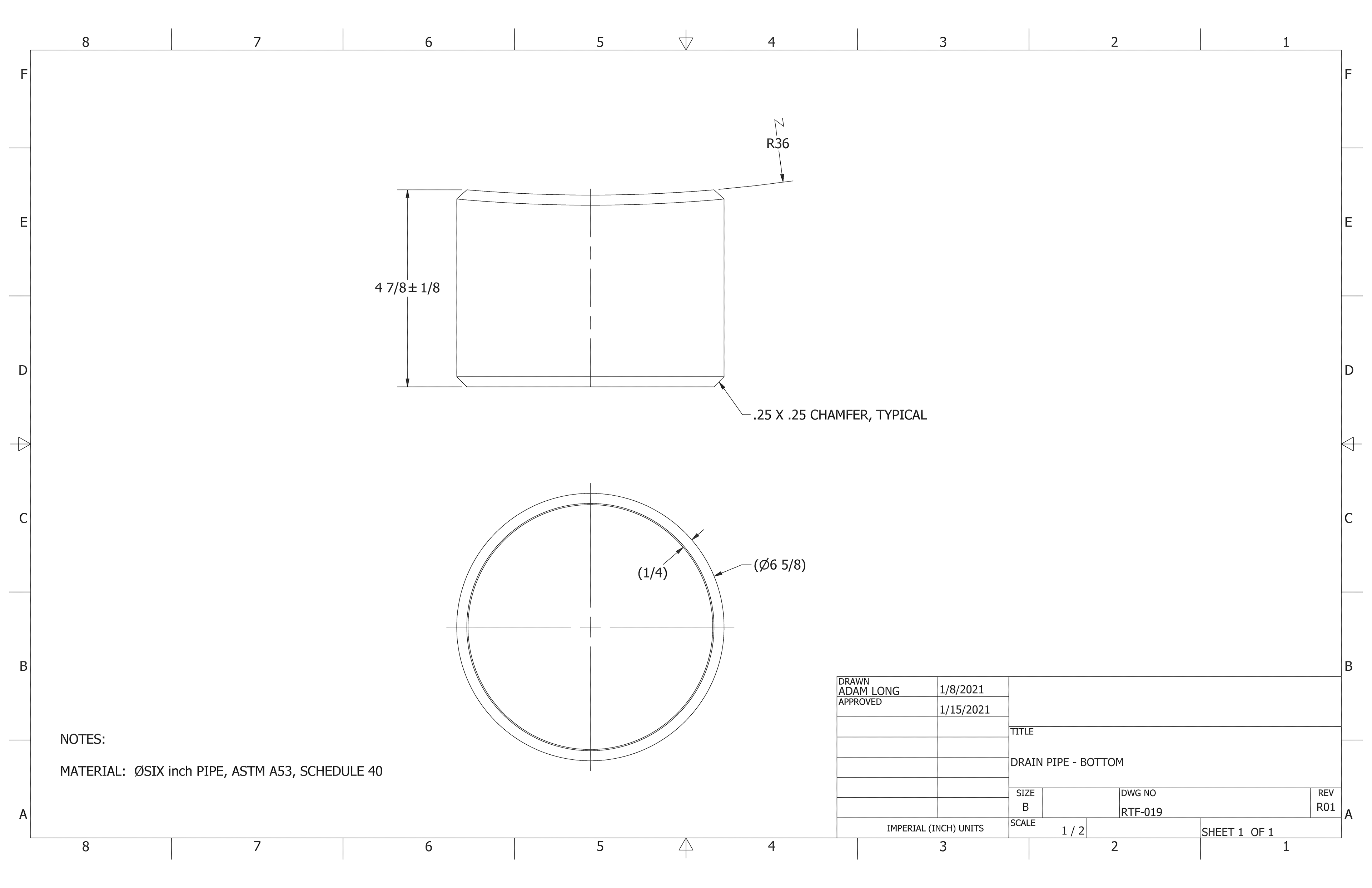
FABRICATION AND DELIVERY
The client used the drawings to source material, buy commercial-off-the-shelf parts, and show manufacturing personnel how to fabricate the tank.
The tank shell was rolled from carbon steel plate, welded, and fitted with end plates. The access hatches were fabricated as sub-assemblies and fitted to pre-cut holes in the top of the shell. Drain pipes and slip-on flanges were added to complete the tank’s basic functionality.
The mixing paddle pieces were strained and bent to geometry specific to the mixing function. These parts were later assembled on-site at the customer’s chocolate manufacturing facility.
The fabricated tank was then blasted and painted to customer requirements.
The mixing paddle pieces were strained and bent to geometry specific to the mixing function. These parts were later assembled on-site at the customer’s chocolate manufacturing facility.
The fabricated tank was then blasted and painted to customer requirements.
The mixing paddles, gear reducer, and motor worked properly at the user’s facility.
The end-user installed the tank in their facility and is mixing chocolate today.
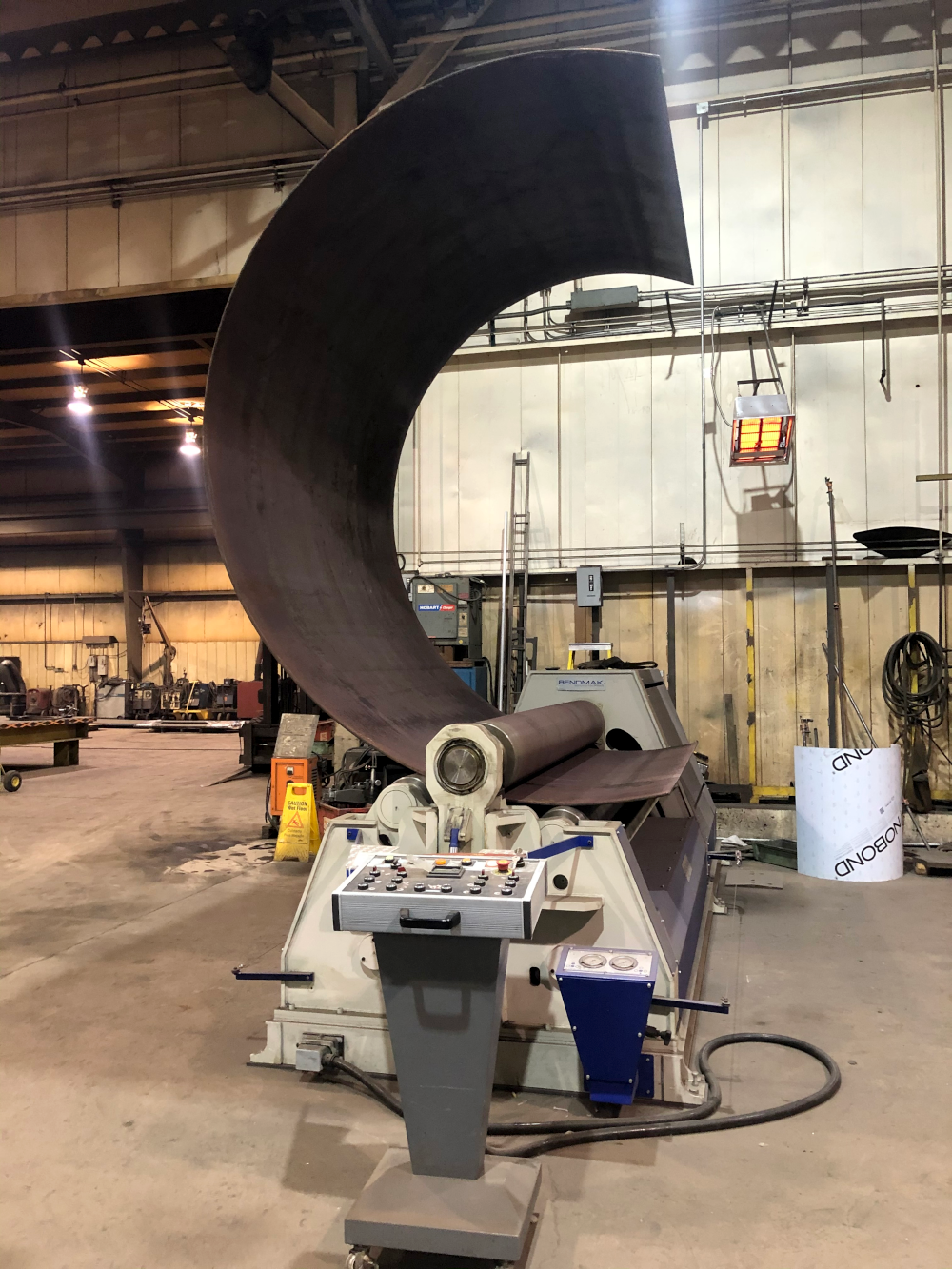