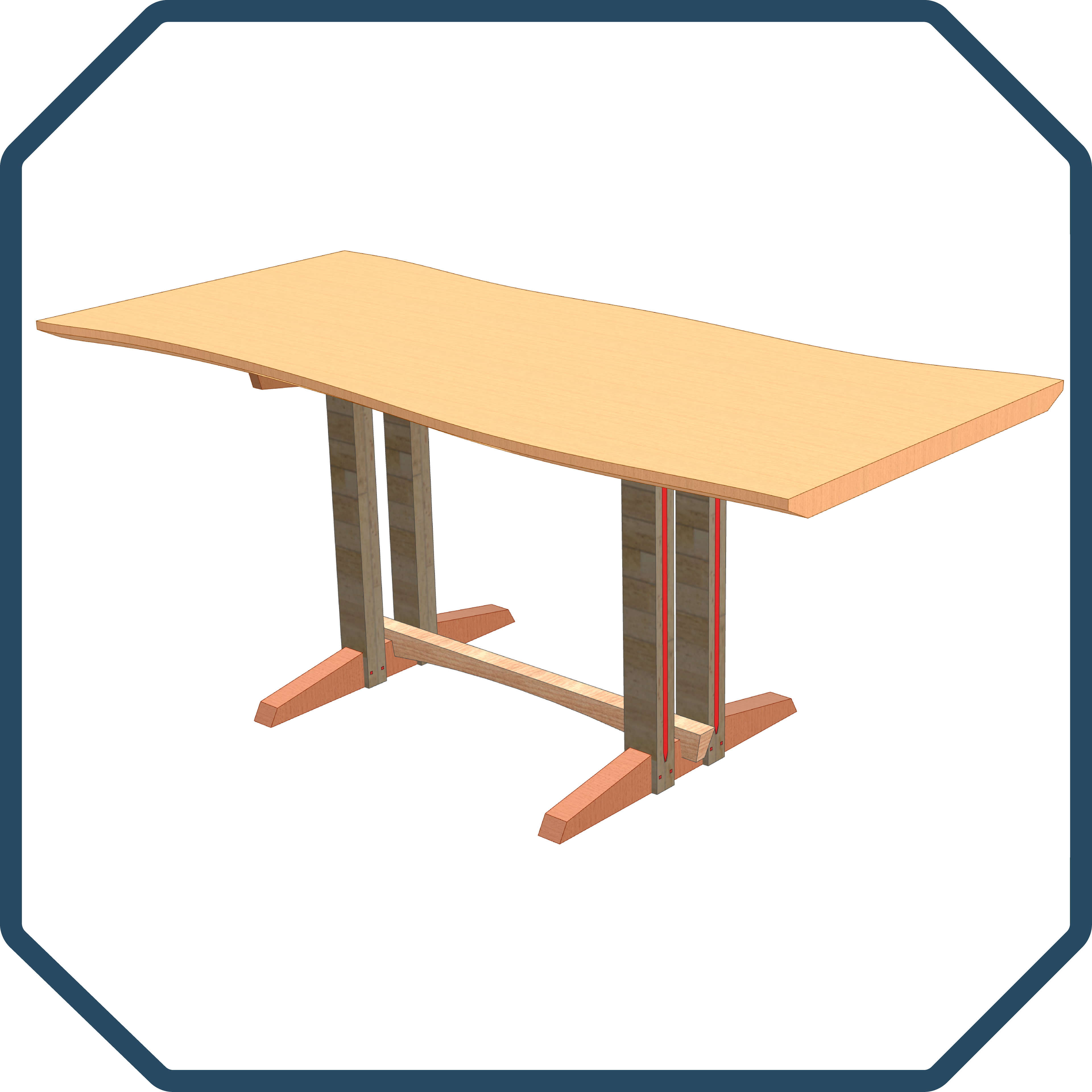
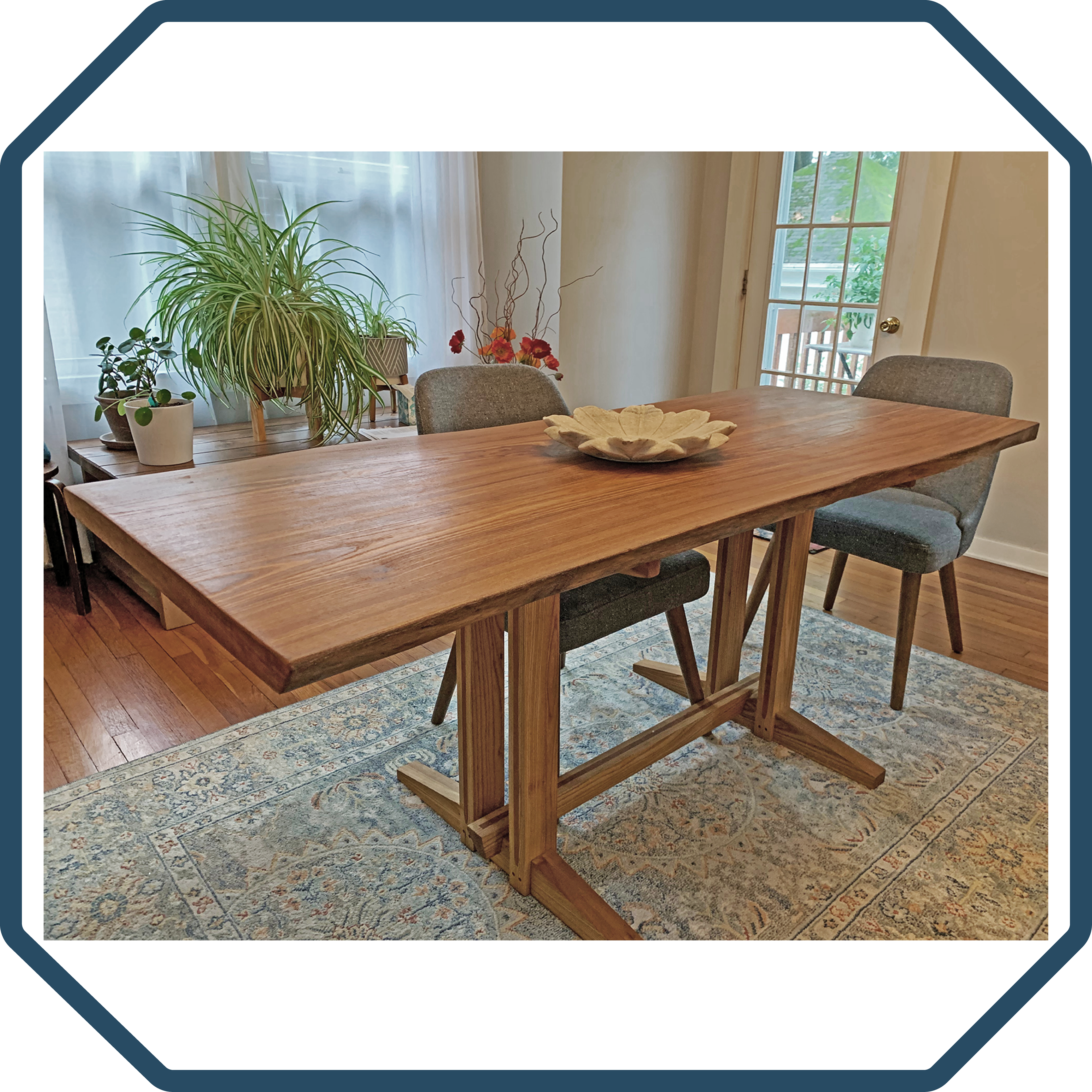
INTRODUCTION
This project showcases Bedrock Design and Craft’s dedication to owning a project from beginning to end. The client desired a bespoke dining table sourced from a material that will eventually be very difficult to obtain because of invasive species - American Elm. Bedrock obtained the elm slab and leg material from a Pennsylvania hardwood supplier and began the process of designing to the client’s specifications.
This dining table is unique in the width - the client’s dining area is mildly constrained and the table needed sized down from the standard 38 inch to about 30 to 32 inch. The width varies with the live edge of the elm slab.
PROJECT SCOPE
Complete set of dining table top-level assembly and detail drawings to obtain client approval and guide fabrication. Inspiration was obtained from previous designs - but the effort started from a clean sheet.
The elm slab was purchased at 2-1/2 inch thickness and needed reduced. A custom slab flattener was designed, procured, built, and used by Bedrock to reduced the thickness of the slab to 1-5/8 inch.
The dining table must be able to be moved in sub-assemblies and then assembled in the client’s home. Knock-down fasteners were sourced and integrated into the design.
DESIGN PROCESS
Using Autodesk Inventor solid modeling, the table design started with reduced table width (30 to 32 inch) and was iterated to reach a length of six feet. This design comfortably seats six adults (four in the center, two on the ends).
The supporting frame was sized to ensure the adults sitting at the ends of the table can comfortably sit fully underneath the ends of the table without hitting their knees against the frame pieces.
The legs were designed to be permanently glued and mechanically pinned using cherry dowels. The connection of each leg to the foot is made using a saddle joint. The connection of each leg to the the table support is similar to a through mortise and tenon - except the support was not reduced in width and the whole piece forms the tenon.
The legs and the bottom spreader include black cherry inlays to provide color contrast with the elm and also link separate structural design elements together.
DRY FITTING TO TEST FORM AND PROPORTION
LEG SUB-ASSEMBLY USING SADDLE JOINTS
LEG SUB-ASSEMBLY FINISHING
SLAB ASSEMBLY AND LEVELING
The elm slab was built by taking a single length of elm, cutting to rough length, squaring one edge on the remaining pieces, and then slotting the length of both the squared edges to accept a full-length cherry spline. The spline increases the surface area of the glue joint and ensures that shear and moment forces can not force the slab axial glue joint apart.
The slab was then reduced in thickness using a custom slab leveler fabricated from MDF and 80/20 extruded aluminum rails, custom router baseplate, and linear bearings. The slab leveler design is unique and an example of Bedrock’s commitment to the project. The tool didn’t exist, so one was crafted to suit the project.
The final slab thickness was reduced from 2-1/2 inch to 1-5/8 inch.
One end of the slab was excessively dry, cracked, split, and required reinforcement. The cracks posed a potential long-term issue. The dry end was grooved and another cherry spline was glued into the end to ensure the cracks do not grow over time.
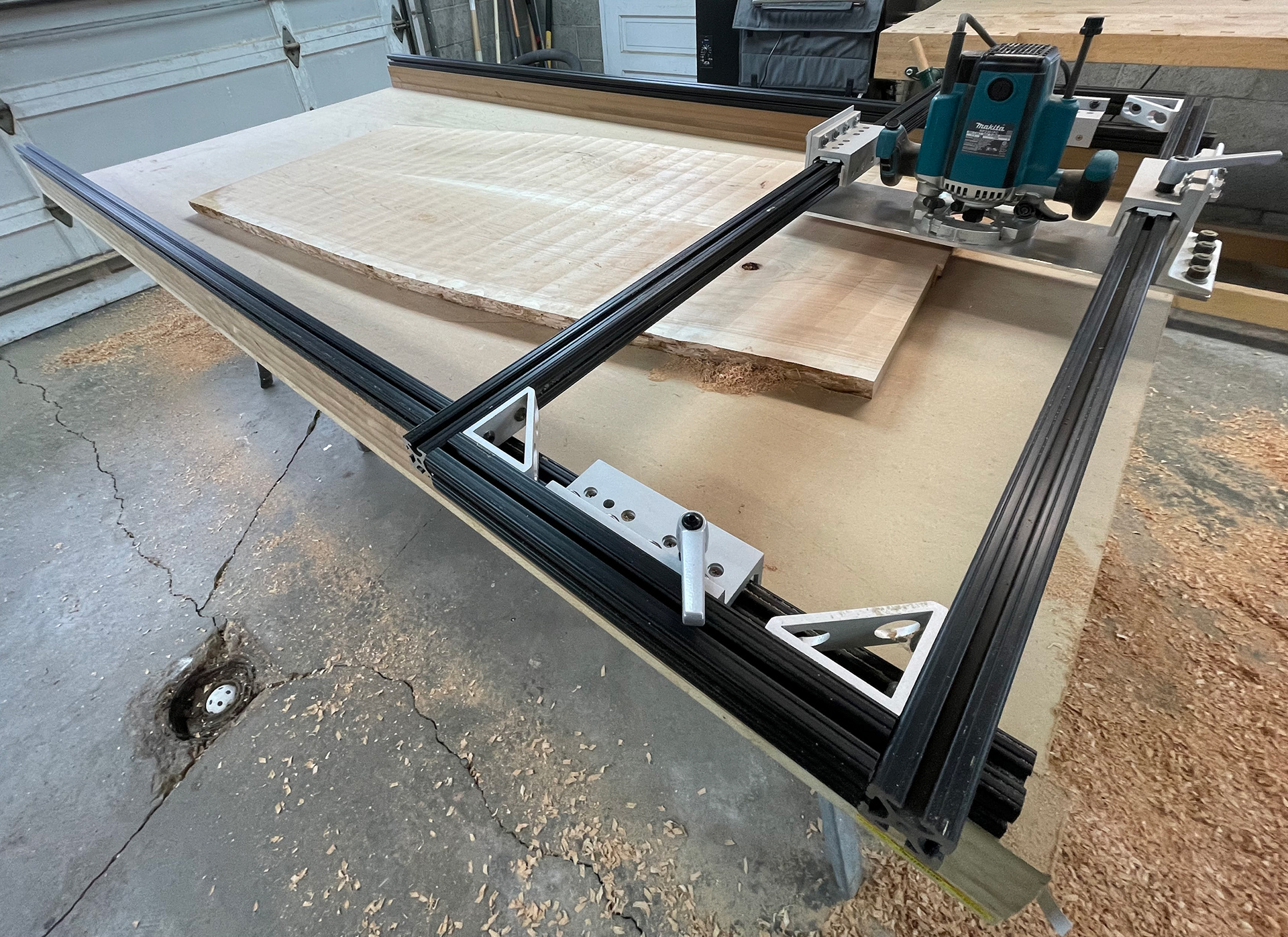
SLAB ENDGRAIN REINFORCEMENT USING SPLINE
FINAL FINISHING
All of the table parts were finished using pure tung oil. No stain was used. The elm slab woodgrain, texture, and color were wildly enhanced by this method of finishing. The resulting color is closer to walnut.
Carnauba wax was was added to the top surface of the table to provide an organic feel and additional protection.